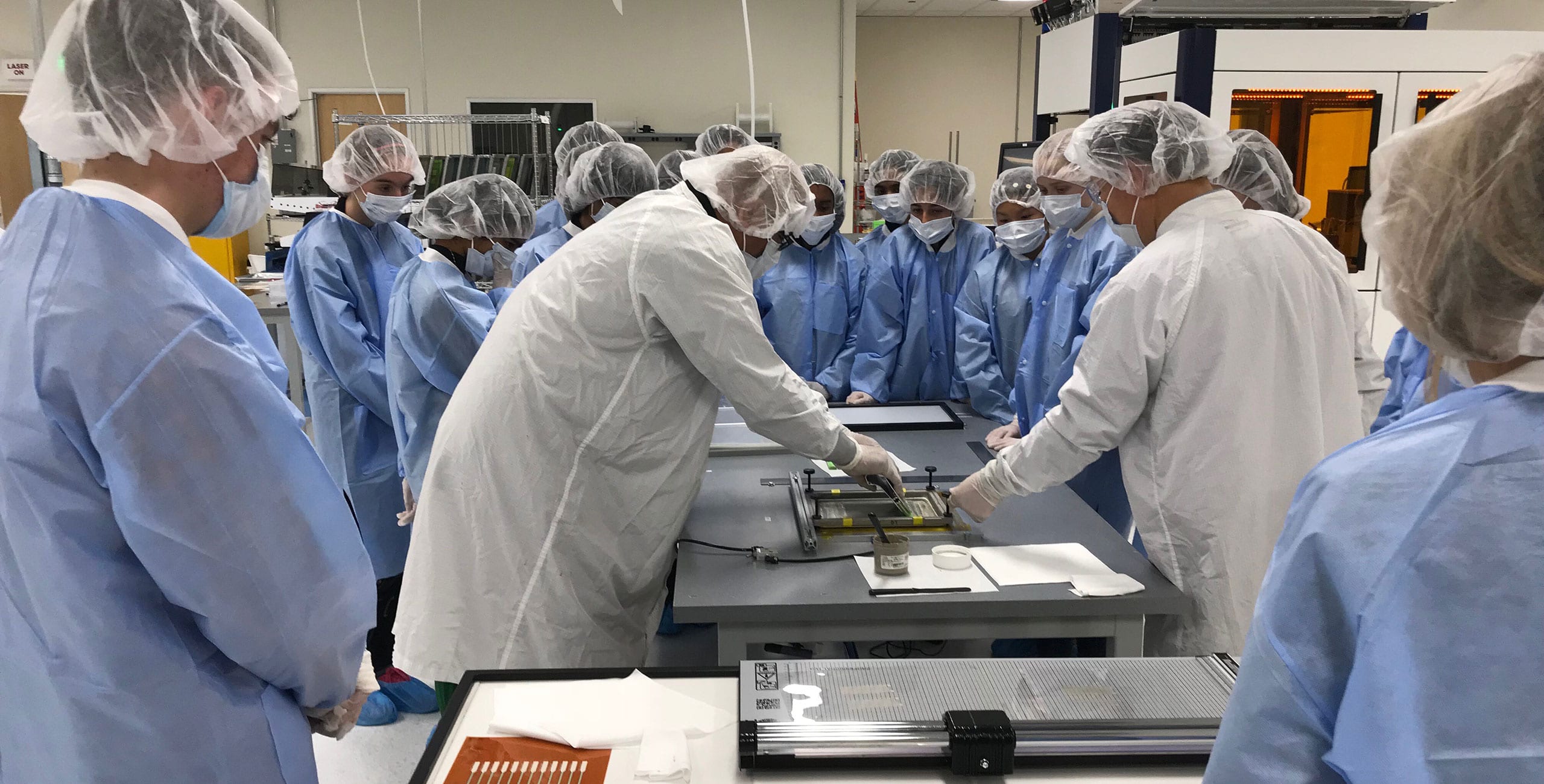
An Interview with Anasuya Adibhatla, Director of Business Development at Fabric8Labs
Question: Anasuya Adibhatla, tell us about your role at Fabric8Labs and the focus of your organization.
Answer: I am a Director of Business Development at Fabric8Labs. I am responsible for creating strategic partnerships with companies and individuals to help Fabric8Labs with our vision and mission to be a manufacturing foundry to various electronic industry companies.
Fabric8Labs, Inc., based in San Diego, California, is revolutionizing manufacturing with its advanced 3D printing technology – Electrochemical Additive Manufacturing (ECAM). Founded in 2015, the company’s proprietary ECAM technology is a key enabler across multiple value chains, such as electronics, medical devices, communications systems, and semiconductor manufacturing. Fabric8Labs is working to broaden the market for metal additive manufacturing by providing advanced manufacturing services that displace traditional manufacturing.
Q: Fabric8Labs is a newer member of NextFlex. What drew you to the FHE manufacturing community and what are you hoping to accomplish through your membership?
A: We were drawn to the FHE manufacturing community by the strong collaborators and shared vision to push the boundaries of electronics with novel designs and manufacturing methods. We have developed an innovative technique to additively manufacture solid metal parts that provides value to the members of NextFlex in thermal management, wireless communications, and electronics components applications. Our mission to be a large-scale manufacturing partner to the members of NextFlex aligns with the opportunities that the community offers and NextFlex’s focus on promoting cutting edge technologies in the electronics industry.
Q: What is a key innovation that will enable widespread adoption of FHE and related technologies, and what application areas are you working in?
A: Our novel ECAM technologies enables 3D printing of fully dense copper and other metals with micro level resolution. This capability allows for high-performance, miniaturized electronics to be manufactured at scale. In addition, the ECAM process operates at room temperature, providing a direct-write capability to print 3D metal structures onto a wide range of substrates including ceramics, PCBs, polyimide, and flexible substrates.
Q: What upcoming activities are you most excited about?
A: The opportunity to participate in and contribute to the community through webinars and events is exciting.
Q: In what ways do you think NextFlex and flexible and hybrid electronics can impact microelectronics manufacturing and / or your own product development?
A: NextFlex is bringing together key players in the industry who have a shared vision for the future of electronics devices. The community can shorten the development cycles for new products by bringing together a wide range of players from product developers to system integrators, to manufacturing partners, and researchers. As FHE continues to mature, we will see increased adoption of new devices that improve the safety, security, and well-being of the global community. Being part of this community will allow us to accelerate the breadth and depth of ECAM adoption in wireless communications and FHE markets.