
- This event has passed.
WORKSHOP: Scalable Manufacturing Methods for Flexible Hybrid Electronics
October 16, 2018 @ 12:00 am - October 18, 2018 @ 12:00 am
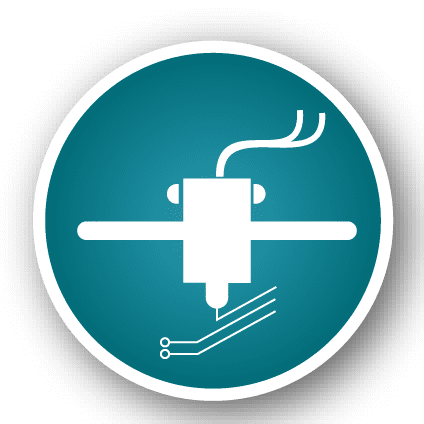
RegisterAgendaAdditional Information
Presented by: Sponsored by:
Advanced Manufacturing Approaches and Platforms for Accelerating the Commercialization of FHE Devices and Systems
This workshop will address topics related to scalable manufacturing of flexible hybrid electronics — paradigms that may apply from prototype to low volume to high volume production. Particular focus will be given to emerging capabilities in print and roll-to-roll manufacturing, and ecosystem-wide discussions of existing progress and challenges for functional materials, devices, and systems. In addition to general challenges, a look at new devices and application-specific manufacturing requirements will be explored. Processes that benefit from continuous coating, patterning and integration strategies will be discussed, along with challenges and opportunities associated with future process-flows for scaled-up manufacturing. Potential benefits of optimized design, improved reliability, more effective modes of operation, and iterative human testing will also be discussed.
Topics
- FHE Applications: Wearables, IoT, and Asset Monitoring
- FHE Manufacturing: Scalable Printing and Integration
- FHE Processing: Roll to Roll
Preliminary Agenda
Tuesday, October 16
1:00pm to 5:00pm TOURS UMass Amherst Life Sciences Lab
Pre-workshop tours of the Life Sciences Lab to include the following facilities:
- Advanced Print and Roll-to-Roll Manufacturing Demonstration Facility
- Human Test Center
- Advanced Digital Design and Fabrication Facility
5:30pm to 8:30pm WELCOME RECEPTION Courtyard Marriott, Hadley, MA
Mingle with FHE manufacturers, designers, and developers and prepare for discussions that will take place during the workshop.
Wednesday, October 17
8:00am to 5:40pm WORKSHOP GENERAL SESSION UMass Amherst Life Sciences Lab Room S330-340
8:00am REGISTRATION and BREAKFAST Room S320
8:30am INTRODUCTION and WELCOME RoomS330-S340
“Introduction to Scalable Manufacturing Methods for Flexible Hybrid Electronics” NextFlex
[showhide type=”Marsh1″ more_text=”Jason Marsh, Director of Technology — Click for Bio” less_text=”Jason Marsh, Director of Technology” hidden=”yes”]
|
“Welcome to UMass Amherst” UMass Amherst
[showhide type=”Reinhart” more_text=”Dr. Peter H. Reinhart, Founding Director, Institute for Applied Life Sciences at UMass Amherst — Click for Bio” less_text=”Dr. Peter H. Reinhart, Founding Director, Institute for Applied Life Sciences at UMass Amherst” hidden=”yes”]
As head of neurodegeneration at Wyeth/Pfizer he directed a portfolio of drug development programs in Alzheimers disease, Parkinsons disease, neuromuscular diseases and stroke/regeneration, and developed more than a dozen small molecules, antibodies, and vaccines. During his leadership, Wyeth Neuroscience was named a Top 10 Pipeline Company for four consecutive years by R&D Directions. As head of neurodegeneration at Cognet Neuroscience, Dr. Reinhart initiated research programs in Huntingtons, Alzheimers and Parkinsons disease, and developed a novel neuronal drug screening platform. Serving as a tenured professor of neuroscience at Duke University Medical Center, Dr. Reinhart investigated the contribution of ion channel dysfunction in neurological and respiratory disorders. He completed postdoctoral training at the University of Tubingen, as a Humboldt fellow, and at Brandeis University, studying ion channel plasticity. Dr. Reinhart received his Ph.D. from the Australian National University, working on intracellular Ca2+ homeostasis and mitochondrial function. Dr. Reinhart serves on the Scientific Advisory Board for the Michael J. Fox Foundation and EDENI and as an editor for multiple neuroscience journals.[/showhide] |
8:40am SESSION I: FHE APPLICATIONS AND PRODUCTS-WEARABLE AND HUMAN HEALTH MONITORING
“Introduction to Session I” Air Force Research Laboratory
[showhide type=”Leever” more_text=”Benjamin Leever, Acting Technical Director, Manufacturing & Industrial Technologies Materials & Manufacturing Directorate, AFRL — Click for Abstract & Bio” less_text=”Benjamin Leever, Acting Technical Director, Manufacturing & Industrial Technologies Materials & Manufacturing Directorate, AFRL” hidden=”yes”]
BioBenjamin Leever’s primary roles are Advanced Development Team Leader at AFRL and Government Chief Technology Officer of NextFlex, a $170M public-private partnership established to create a domestic manufacturing ecosystem in flexible hybrid electronics. In support of AFRLs external investments in flexible electronics and biomaterials, Dr. Leever determines technical strategy, manages AFRL contracts, and establishes industrial, academic, and governmental collaborations. He also leads the directorates Energy Integrated Product Team and represents the directorate on numerous domestic and international power & energy and additive manufacturing working groups. Prior to assuming his current duties, Dr. Leever led a research team focused on the development and modeling of multifunctional materials for structural power applications. Dr. Leever began his career at AFRL in the Manufacturing Technology Division, where he managed programs related to electro-optics systems. He earned a B.S. in Chemical Engineering from the University of Cincinnati and a Ph.D. in Materials Science & Engineering from Northwestern University.[/showhide] |
“Soft Wearable Systems with Physiological Monitoring and Biochemical Sensing Capabilities”Epicore Biosystems
[showhide type=”Raj” more_text=”Milan Raj, VP, Technology and Operations — Click for Abstract & Bio” less_text=”Milan Raj, VP, Technology and Operations” hidden=”yes”]
Bio Milan Raj obtained the B.S. and M.S. degrees in Electrical Engineering from the University of Michigan, Ann Arbor, and the University of California, Irvine, in 2003 and 2006, respectively. Specializing in analog and RF circuit design, Milan has 15+ years of research and product development experience and extensive background spearheading novel, wearable technologies for real-time biometrics. While at MC10, Inc., he managed a multi-disciplinary team of engineers to advance and develop novel electronic systems that make intimate contact with the skin for digital health applications. These efforts produced robust, reliable wearable systems that were manufactured at high yield and commercialized. Prior to this, he was an Associate Staff member at MIT Lincoln Lab, developing novel system architectures for state-of-the-art radar applications. In his current role as Vice President of Technology and Operations at Epicore Biosystems, Milan leverages his broad industry experience, driving projects from their initial prototype stages to system platform technologies that incorporate best engineering and manufacturing practices. His current efforts for the NextFlex PC 3.7 Program drive the convergence of FHE systems and microfluidic platforms to accelerate the development of multi-modal biosensors for personalized health and wellness.[/showhide] |
“Towards Conformal/Stretchable Sensor Systems for Continuous Monitoring of Tissue Hypoxia”Profusa and North Carolina State University
[showhide type=”Profusa” more_text=”Natalie Wisniewski, Co-Founder and Chief Technology Officer, andVladimir Pozdin, Postdoctoral Research Scholar — Click for Abstract & Bio” less_text=”Natalie Wisniewski, Co-Founder and Chief Technology Officer, andVladimir Pozdin, Postdoctoral Research Scholar” hidden=”yes”] Abstract Body chemistries can be continuously monitored through the use of novel tissue-integrating sensors.The sensors are passive hydrogels engineered to change optical properties in the presence of various analytes (e.g. oxygen, glucose, lactate). The hydrogels are injected under the skin and an external wearable reader monitors the hydrogels and relays the analyte concentration to a cell phone. Our first approved oxygen sensing hydrogel received CE Mark for commercialization in the European Union in 2016. Our oxygen sensing technology can be applied to a multitude of medical application such critical limb ischemia, sleep apnea, reconstructive surgery as well as monitor health states such as exercise physiology and pilot readiness. To provide an optimal wearability, Profusa has partnered with NC State with the goal of converting Profusas current wearable hard patch reader into a conformal/stretchable format. In this presentation, we will discuss Profusas oxygen sensing platform, our ongoing effort to develop a conformal/stretchable reader, and, finally, some of the challenges in manufacturing and scale-up. Bios
Dr. Wisniewski earned engineering degrees from Purdue University (B.S. in Chemical Engineering where she conducted four years of hydrogel research) and Duke University (Ph.D. in Biomedical Engineering where she elucidated mechanisms and effects of biofouling of implantable biosensors). She worked in R&D and manufacturing for consumer products at Kimberly-Clark Corporation and in management consulting with McKinsey & Company. Before starting Profusa she ran her own consulting firm in the San Francisco Bay Area specializing in technical, clinical and regulatory strategy. She currently serves on the Board of Directors and as Chief Technology Officer at Profusa.
|
“Manufacturing of disposable wearable patient monitoring devices” General Electric
[showhide type=”Alizadeh” more_text=”Azar Alizadeh, Principal Scientist — Click for Abstract & Bio” less_text=”Azar Alizadeh, Principal Scientist” hidden=”yes”]
Bio NextFlex Fellow Dr. Azar Alizadeh is a senior material scientist at GE Global Research where she develops materials and processes for applications such as health-monitoring sensors, non-icing surfaces, nano-enabled media storage, and optoelectronic devices. She holds a PhD in physics and has extensive experience in the field of nano-bio-manufacturing and has led numerous cross-functional teams during her tenure at GE Global Research, including the NBMC “Wearable device for dynamic assessment of hydration status;” the US Army “A wearable physiological monitoring system for assessment of hemodynamic state;” and the AFRL study of “Sensor systems for warfighter health and performance monitoring and augmentation.” She also serves as a co-lead on the NextFlex Human Health Monitoring Systems Technical Working Group. Dr. Alizadeh has 45 peer reviewed publications and 13 US patents/patent applications.[/showhide] |
10:20am SESSION II: FHE APPLICATIONS AND PRODUCTS-IOT AND ASSET MONITORING
“Introduction to Session II” NextFlex
[showhide type=”Miller1″ more_text=”Scott Miller, Director of Strategic Programs — Click for Abstract & Bio” less_text=”Scott Miller, Director of Strategic Programs” hidden=”yes”]
Bio As the director of strategic programs, Scott is responsible for overseeing US government projects, building relationships with DARPA and the National Science Foundation and building and managing critical relationships with the medical, avionics and pharmaceutical industries. Most recently, he was the manager of GE Global Researchs Material System Lab where he led a multidisciplinary team developing and delivering material technologies and processes for GE products and services. Prior, he led GEs Nanostructures & Surfaces Lab where he oversaw a multidisciplinary team of researchers in the field of nano-enabled materials, serving GEs Healthcare, Aviation, Power, and Oil & Gas Businesses. Scott holds eight patents, was the Founding Board Chair of the Nano-Bio Manufacturing Consortium (NBMC), and is a member of the American Chemical Society. He has a PhD in Chemical Engineering from Princeton University and a Bachelor of Science in Chemical Engineering from the University of Delaware. |
“FHE Based Designs and Fabrications for Intelligent Assets” United Technologies Research Center
[showhide type=”Dardona” more_text=”Sameh Dardona, Associate Director, Research & Innovation — Click for Abstract & Bio” less_text=”Sameh Dardona, Associate Director, Research & Innovation” hidden=”yes”]
Bio Sameh Dardona received the B.S. degree from Birzeit University, West Bank, Palestine, in 1998, the M.S. degree from Temple University, Philadelphia, PA, USA, in 2002, and the Ph.D. degree from the Georgia Institute of Technology, Atlanta, GA, USA, in 2006, all in applied physics. He joined the United Technologies Research Center (UTRC), in 2006 as a senior scientist and is currently an associate director for research and innovation. He is leading the printed electronics initiative with responsibly to integrate advanced sensors into aerospace, energy, and building industries assets. His research interests include electronics additive manufacturing, advanced and embedded sensors, sensor network, physics-based device modeling, and designs for additive manufacturing.[/showhide] |
US Army ARDEC
[showhide type=”Zunino” more_text=”James L. Zunino III, Materials Engineer / ARDEC Project Officer — Click for Abstract & Bio” less_text=”James L. Zunino III,Materials Engineer / ARDEC Project Officer” hidden=”yes”]
Bio Mr. James Zunino is a Materials Engineer within the Armaments Engineering Analysis & Manufacturing Directorate, located at the U.S Army Research, Development and Engineering Center (ARDEC), Picatinny Arsenal, NJ. He serves as the subject matter expert on additive manufacturing, smart coatings, flexible electronics, materials printing, and novel ink development at ARDEC. He provides technical support to ARDEC’s broad mission and is responsible for designing, testing, and overseeing related technologies. Mr. Zunino works with customers and end users to develop systems and provide solutions to help meet their requirements and needs. He holds a Master’s of Business Administration and a B.S in Chemical Engineering from New Jersey Institute of Technology. He has received numerous awards including: Thomas Alva Edison Patent Award, Department of the Army Research and Development Achievement Award, IDTechEx Academic R&D, as well as other DoD and Industry awards.[/showhide] |
NextFlex
[showhide type=”Marsh2″ more_text=”Jason Marsh, Director of Technology — Click for Abstract & Bio” less_text=”Jason Marsh, Director of Technology” hidden=”yes”] Abstract Coming soon. Bio Jason Marsh is responsible for setting the technical direction of NextFlex, including managing Technical Council activities. Prior to joining NextFlex, Jason worked in Asia, Europe and throughout North America establishing greenfield factories for Kyocera and developing new materials and supply-chain strategies for Insulectro. Jason studied materials science and robotics at Stanford University, and has served on a variety of advisory boards in artificial intelligence, solar power, and agriculture.[/showhide] |
11:30am LUNCH AND KEYNOTE
“The Tech Holy Grail for Exercise in the Heat – Safety/Performance Relevance for the Warfighter, Laborer and Athlete”University of Connecticut
[showhide type=”Casa” more_text=”Douglas Casa, Professor, Department of Kinesiology; CEO, Korey Stringer Institute — Click for Abstract & Bio” less_text=”Douglas Casa, Professor, Department of Kinesiology; CEO, Korey Stringer Institute” hidden=”yes”] Abstract Exercise in the heat provides incredible challenges for the laborer, warfighter and athlete. The performance, physiological, and psychological decrements associated with intense exercise in the heat are well document and can increase the risk of medical issues, sometimes with catastrophic outcome. Additionally, the ability to successfully perform the mission or job or athletic endeavor is perpetually at risk when the stress of the heat is not properly respected and planned for with modifications to policies and procedures. This talk will focus on potential strategies that exist and will hopefully exist in the years to come to enhance the process of performing intense exercise in the heat. Bio For Douglas Casa, the opportunity to maximize athletic performance in the heat and prevent sudden death in sport is the culmination of a life-long path; his passion for the study of exertional heat stroke started in 1985 when he suffered an exertional heat stroke while running a 10K race. This experience motivated what has become his lifes cause: the study of exertional heat stroke, heat illnesses, hydration, and preventing sudden death in sport — his ultimate goal is to find ways to maximize performance in challenging circumstances while working prevent needless tragedy during sport and physical activity. I was fortunate to receive amazing care on-site from the athletic trainer; the EMTs in the ambulance; and at the hospital from the emergency room physicians and nurses. I only survived because of the exceptional care I received. I was just 16 years old at the time, but I have been driven by this experience since that day, Dr. Casa explains when asked about what motivates him. He celebrated his 30th anniversary of surviving his exertional heat stroke on August 8, 2015. In April 2010 Kelci Stringer (Koreys widow), James Gould (Koreys agent), and the NFL asked Dr. Casa to develop and run the Korey Stringer Institute (KSI) at the University of Connecticut. Korey was an All-Pro offensive tackle for the Minnesota Vikings of the NFL. He died from exertional heat stroke in August 2001. The mission of the KSI (ksi.uconn.edu) is to provide research, education, advocacy, and consultation, to maximize performance, optimize safety, and prevent sudden death for the athlete, warfighter, and laborer. Additionally, he is the editor of a book titled: Preventing Sudden Death in Sport and Physical Activity (2nd edition, 2017), published by Jones & Bartlett in cooperation with the American College of Sports Medicine. His book titled Sports and Physical Activity in the heat: Maximizing Performance and Safety was published by Springer in the summer of 2017.[/showhide] |
12:50pm SESSION III: INTEGRATION AND PROCESS SCALE-UP, PART ONE
“Introduction to Session III” NextFlex
[showhide type=”Marsh3″ more_text=”Jason Marsh, Director of Technology — Click for Abstract & Bio” less_text=”Jason Marsh, Director of Technology” hidden=”yes”]
Bio Jason Marsh is responsible for setting the technical direction of NextFlex, including managing Technical Council activities. Prior to joining NextFlex, Jason worked in Asia, Europe and throughout North America establishing greenfield factories for Kyocera and developing new materials and supply-chain strategies for Insulectro. Jason studied materials science and robotics at Stanford University, and has served on a variety of advisory boards in artificial intelligence, solar power, and agriculture.[/showhide] |
“A New Roll-to-Roll Manufacturing Line to Produce Multifunctional Films for Ultrasensitive Sensors” Purdue University
[showhide type=”Cakmak” more_text=”Miko Cakmak, Reilly Professor of Materials Engineering & Mechanical Engineering — Click for Abstract & Bio” less_text=”Miko Cakmak, Reilly Professor of Materials Engineering & Mechanical Engineering” hidden=”yes”]
Bio Dr. Cakmak received his BS in Chemical Engineering from Technical University of Istanbul and MS and PhD in Polymer Engineering from University of Tennessee, Knoxville. He was one of the founders of Polymer Engineering Department at University of Akron where he was named Harold A. Morton Chair and Distinguished Professor of Polymer Engineering. He recently was the founding director of the National Polymer Innovation Center where he developed roll to roll manufacturing lines for functional polymer films for a range of applications including membranes for batteries, biomedical devices such as artificial pancreas, slow drug release platforms, flexible transparent electrodes for flexible electronics and flexible sensors.[/showhide] |
“Progress Toward a Self-Aligned, Roll-to-Roll Manufacturing Process for Printed Circuitry” University of Minnesota
[showhide type=”Frisbie” more_text=”C. Daniel Frisbie, Distinguished McKnight University Professor and CEMS Department Head — Click for Abstract & Bio” less_text=”C. Daniel Frisbie, Distinguished McKnight University Professor and CEMS Department Head” hidden=”yes”]
Bio C. Daniel Frisbie is Distinguished McKnight University Professor and Head of Chemical Engineering and Materials Science at the University of Minnesota. He obtained a PhD in physical chemistry at MIT in 1993 and was an NSF Postdoctoral Fellow at Harvard. His research focuses on materials for printed electronics, including organic semiconductors and their applications in devices such as transistors and electrochromic displays. Research themes include the synthesis of novel organic semiconductors, structure-property relationships, organic device physics, and the application of scanning probe techniques. Recent efforts also include new manufacturing approaches for flexible electronics and the use of gel electrolytes as high capacitance gate insulators in OTFTs to lower drive voltages. From 2002-2014, Frisbie led a multi-investigator effort in Organic Optoelectronics at the University of Minnesota, sponsored by the Materials Research Science and Engineering Center (MRSEC) program of the NSF. He was the lead investigator on a Multi-University Research Initiative (MURI) grant funded by the Office of Naval Research from 2011-2017 for development of a roll-to-roll printed electronics manufacturing platform.[/showhide] |
“The requirements and challenges of large scale manufacturing of flexible hybrid electronics and their applications” Molex
[showhide type=”Spitzer” more_text=”Justin Spitzer, Sales and Marketing Manager, Global Sales and Business Development — Click for Abstract & Bio” less_text=”Justin Spitzer, Sales and Marketing Manager, Global Sales and Business Development” hidden=”yes”]
Bio Justin Spitzer has a degree in mechanical engineering from Florida Tech and has worked in electronics for over 25 years with over 17 years focused on flexible circuitry. Starting with printed circuits in user interface products, Justin has been part of Molexs expansion into flexible copper circuits and printed silver circuitry. Currently, Justin is the global sales and marketing manager for Molexs Flexible Circuit Solutions and Sensor Systems product line, focusing on printed electronics and the integration of wireless and sensor solutions.[/showhide] |
“Manufacturer’s Influence in Technology Success” FLEXcon, Inc.
[showhide type=”Sullivan” more_text=”William Sullivan, Vice President, Performance Products for Spencer — Click for Abstract & Bio” less_text=”William Sullivan, Vice President, Performance Products for Spencer” hidden=”yes”]
Bio William Sullivan is Vice President, Performance for Spencer, MA-based FLEXcon Company, Inc., and oversees a Business Team (Performance Products) that is responsible for the development, marketing and commercialization of high-performance adhesives, functional coatings, film castings and the creation of functional microstructures. Author of nationally published articles and books primarily on functional microstructure, he has years of experience assisting startup companies and enterprises with bringing their concepts and ideas to commercial reality.[/showhide] |
2:50pm SESSION IV: INTEGRATION AND PROCESS SCALE-UP, PART TWO
“Introduction to Session IV” UMass Amherst
[showhide type=”Morse” more_text=”Jeff Morse, Director Advanced Print and Roll-to-Roll Manufacturing Facility — Click for Abstract & Bio” less_text=”Jeff Morse, Director Advanced Print and Roll-to-Roll Manufacturing Facility” hidden=”yes”]
BioJeff Morse is the Managing Director of the National Nanomanufacturing Network, part of the NSF Center for Hierarchical Manufacturing, at the University of Massachusetts, Amherst. In addition, Jeff is the Director of the Advanced Print and Roll-to-Roll Manufacturing Facility at UMass Amherst Previously Jeff was a Senior Scientist in the Center for Micro and Nano Technology at Lawrence Livermore National Laboratory. He received his BS (1983) and MS (1985) Degrees in Electrical Engineering from the University of Massachusetts, and a PhD (1992) in Electrical Engineering from Stanford University. His interests and expertise includes semiconductor devices, advanced micro/nanofabrication processes, microelectromechanical systems (MEMS), biosensors, microfluidics, and micro-power sources.[/showhide] |
“Printing fine lines from NIL to Gravure with Lessons from the Gravure Association of America” Carpe Diem Technologies
[showhide type=”Berg” more_text=”John Berg, CEO — Click for Abstract & Bio” less_text=”John Berg, CEO” hidden=”yes”] Abstract This presentation will share insights in evolving capability for high volume fine pitch conductor printing. It will highlight Carpe Diem’s compact gravure coater, printer, and flexo unit and then the convergence with Nano Imprint Lithography. Some take-away’s from the October 10, 2018, GAA annual meeting at which the presenter was a featured speaker and attendee. Key insights necessary for repeatable commercial performance will be identified. Finally, mastering for NIL and Gravure as key enablers will be presented. Bio John S. Berg holds engineering degrees from UMass Dartmouth and MIT. Carpe Diem Technologies is his third start-up. He previously lead Firefly Technologies, Inc. and Aprilis, Inc. after holding management and engineering positions at Digital Equipment Corp., Quantum, and Zygo. Berg is named on 35 patents from optical data storage to roll to roll nano imprint technology. At the 2017 FlexTech conference he presented an update on the R2R equipment and technology suite Carpe Diem developed with the UMass Roll to roll and Life Sciences facility. The technologies and innovations presented included: spatial ALD, nano imprint and photo lithography, and interferometric alignment – all for the manufacture of complex devices or nano-enabled features on flexible substrates. Building on the work with UMass, sponsorship from the State, and collaborations with well-established manufacturers, Carpe Diem has become known for their differentiated capability relative to R2R NIL. Carpe Diem is the hub of a state and national ecosystem for the development and mass production of nano-imprinted and micro structures for flexible hybrid electronic and large area high volume applications.[/showhide] |
“High Throughput Printed Electronics Application Challenges, a Printer/Converter Contract Manufacturer Perspective” Tapecon
[showhide type=”Davis” more_text=”Steve Davis, President — Click for Abstract & Bio” less_text=”Steve Davis, President” hidden=”yes”] Abstract Contract manufacturers with specialized printing and converting capability face challenges as they assess business opportunities to meet the manufacturing requirements of emerging FHE products. The presentation will cover challenges and approaches in assessing new opportunities for high throughput printed electronics applications and the implications that R2R printing processes (flexographic and flatbed screen) have on overall throughput. Bio Steve Davis is the President at Tapecon, Inc., a 5 generation, family owned contract manufacturer based in Buffalo, New York. Tapecon works with product teams to improve market competitiveness by manufacturing functional graphics, materials and complete products to improve look, feel and usability. Tapecon offers a broad scope of services in converting and specialized printing technologies for product branding, printed & flexible electronics, and disposable medical device manufacturing. Steve’s efforts have created a progressive culture of innovation at Tapecon over his thirteen years with the company.[/showhide] |
“Strengths, Weaknesses and Opportunities for Scalable Printing of Energy Devices” University of Washington
[showhide type=”MacKenzie” more_text=”Devin MacKenzie, Washington Research Foundation Professor of Clean Energy — Click for Abstract & Bio” less_text=”Devin MacKenzie, Washington Research Foundation Professor of Clean Energy” hidden=”yes”]
Bio Dr. MacKenzie is the Washington Research Foundation (WRF) Professor of Clean Energy and an Associate Professor of Materials Science and Engineering and Mechanical Engineering at the University of Washington. Dr. MacKenzie directs the Washington Clean Energy Testbeds, an open access laboratory with world-class printed electronics and energy device fabrication and testing capabilities with 190 industrial and academic users. Devin also oversees the WRF Roll-to-Roll (R2R) facility houses a multilayer R2R system with flexographic, gravure, screen-printing and high precision film coating systems coupled to 7.5m ovens, IR heating and photonic sintering systems. Devin has 19 years of experience in printed electronics and holds director and advisory board positions at FOM Technologies, EnergSoft, and Imprint Energy, where he was a co-founder and CEO commercializing printed batteries. As CTO of Add-Vision, he directed printed flexible OLEDs R&D. At Kovio, an MIT spin out, he led printed Si RF device and process integration. Devin also co-founded the world’s first printed electronics company, Plastic Logic, as a postdoc in Physics at the University of Cambridge and was a research associate at Bell Labs. Dr. MacKenzie has over 200 patents and publications and earned PhD, MS, and SB degrees from the University of Florida and MIT.[/showhide] |
“Addressing Integration Density and Materials Challenges for Roll-to-Roll Fabrication of Intelligent Devices” UMass Amherst
[showhide type=”Watkins” more_text=”Jim Watkins, Professor — Click for Abstract & Bio” less_text=”Jim Watkins, Professor” hidden=”yes”]
Bio Jim Watkins is a Professor of Polymer Science and Engineering and Director of the Institute for Hierarchical Manufacturing, which continues from a ten-year National Science Foundation Nanoscale Science and Engineering Center (NSEC) at the University of Massachusetts, Amherst. Professor Watkins received his B.S. and M.S. degrees in Chemical Engineering from the Johns Hopkins University and his Ph.D. in Polymer Science and Engineering from the University of Massachusetts. He joined the Chemical Engineering faculty at UMass in 1996 and the Polymer Science and Engineering Faculty in 2005. Professor Watkins has authored more than 100 papers in leading journals and has presented more than 200 invited lectures. He has out licensed technology in electronics, energy storage and advanced optics. Prof. Watkins is a recipient of the Camille Dreyfus Teacher-Scholar Award and a David and Lucile Packard Foundation Fellowship for Science and Engineering. He is a fellow of the American Physical Society.[/showhide] |
4:20pm SESSION V: PANEL – CHALLENGES AND OPPORTUNITIES IN SCALE-UP: FROM MATERIALS AND EQUIPMENT TO PROCESS INTEGRATION
Moderator, NextFlex
[showhide type=”Miller2″ more_text=”Scott Miller, Director of Strategic Programs — Click for Bio” less_text=”Scott Miller, Director of Strategic Programs” hidden=”yes”]
|
Panelist, FUJIFILM Dimatix
[showhide type=”Dadok” more_text=”Lou Dadok, Business Development Manager — Click for Bio” less_text=”Lou Dadok, Business Development Manager” hidden=”yes”]
|
Panelist, NovaCentrix
[showhide type=”Larson” more_text=”Rick Larson, Technical Business Development / Strategic Account Management — Click for Bio” less_text=”Rick Larson, Technical Business Development / Strategic Account Management” hidden=”yes”]
|
Panelist, Flex
[showhide type=”Nugent” more_text=”Yolita Wildman Nugent, Director of Textiles, Program Management — Click for Bio” less_text=”Yolita Wildman Nugent, Director of Textiles, Program Management” hidden=”yes”]
In Boston she is the founding leader of the Center of Competence of Textiles, that has a regional focus on idea generation, design and prototyping for Flex customers. It is here where she has built a team of cross-disciplined textile designers, scientists and engineers that focus on the merger of textile technologies and electronics within a soft-architecture system.[/showhide] |
Panelist, Butler Technologies
[showhide type=”Tripodi” more_text=”Nadine Tripodi, Co-Founder and President — Click for Bio” less_text=”Nadine Tripodi, Co-Founder and President” hidden=”yes”]
[/showhide] |
Eastman Chemical Company
[showhide type=”Stoessel” more_text=”Chris H. Stoessel, PhD, Sr. Manager, Process Development — Click for Bio” less_text=”Chris H. Stoessel, PhD, Sr. Manager, Process Development” hidden=”yes”]
|
5:40pm to 7:30pm NETWORKING RECEPTION and POSTER SESSION Room S320
Network with attendees and participate in the poster session where students and NextFlex members show off their latest FHE projects.
Thursday, October 18
8:00am to 12:00pm BREAKOUT SESSION* UMass Amherst Life Sciences Lab Rooms S330, S340
*Restricted to NextFlex Observer-Level members and above.
The workshop concludes with facilitated breakout discussions for NextFlex members based on the topics below that will generate actionable tasks giving attendees a chance to influence upcoming funded project calls.
8:00am REGISTRATION and BREAKFAST Room S320
8:30am ORIENTATION and KEYNOTE RoomS330-S340
“Breakout Orientation” NextFlex
[showhide type=”Marsh4″ more_text=”Jason Marsh, Director of Technology — Click for Bio” less_text=”Jason Marsh, Director of Technology” hidden=”yes”]
|
KEYNOTE “Monolithically-Integrated Wearable Electronics” UMass Amherst
[showhide type=”Andrews” more_text=”Trisha Andrews, Director, Wearable Electronics Lab; Assistant Professor of Chemistry and Materials Engineering — Click for Abstract & Bio” less_text=”Trisha Andrews, Director, Wearable Electronics Lab; Assistant Professor of Chemistry and Materials Engineering” hidden=”yes”]
Bio Trisha is the Director of the Wearable Electronics Lab at the University of Massachusetts Amherst. The WELab produces textile electronics that maintain the feel, stretchability, breathability and light weight of common fabrics. We use vapor phase coating chemistry to imperceptibly transform mass-produced threads and textiles, such as cotton, silk, nylon and wool, into electronic components suitable for portable energy harvesting and storage, temperature regulation and health monitoring. Trisha is a David and Lucille Packard Foundation Fellow, and an Air Force Young Investigator, a 3M Nontenured Faculty Award winner, and was named as one Forbes magazine 30 Under 30 Innovators in Energy.[/showhide] |
9:00am BREAKOUTS Room S330-S340
- FHE Applications: Wearable and Human Health Monitoring Room s330
- FHE Applications: IoT and Asset Monitoring in Room S340
12:00PM END
Who Should Attend
- Print and R2R Manufacturers
- Flexible Electronic Device Developers
- Wearable & Medical Device Developers, Healthcare Professionals
- Smart Textile Designers
- FHE Technology Innovators who are interested in connecting with potential government customers and OEMs
- Manufacturers of R2R and other high-throughput tools
Hotel
Hotels located within the vicinity of the workshop include:
- Hampton Inn Hadley-Amherst
- Holiday Inn Express Amherst-Hadley(This hotel located at 400 Russell St, Hadley, MA 01035, also offers a government per diem rate. If you qualify, please call to make your reservation here: (413) 582-0002.)
- Howard Johnson by Wyndham Amherst Hadley
- Or click here for additional options
Fees
Early Bird | Regular | On-Site | |
Member | $ 190 | $ 245 | $ 265 |
Non-Member | $ 300 | $ 370 | $ 390 |
Government* | $ 0** | $ 0** | $ 0** |
Schedule | (8/17/18-9/14/18) | (9/15/18-10/15/18) | (10/16/18-10/18/18) |
*Must register using .mil or .gov email address. No exceptions.
**Government participants can give a cash contribution for each reception and meal. The suggested amounts will be included in your confirmation email.
Cant view the registration form? Click the “Register” button above or please contact Laura Castellano at 408-797-2247 to register.