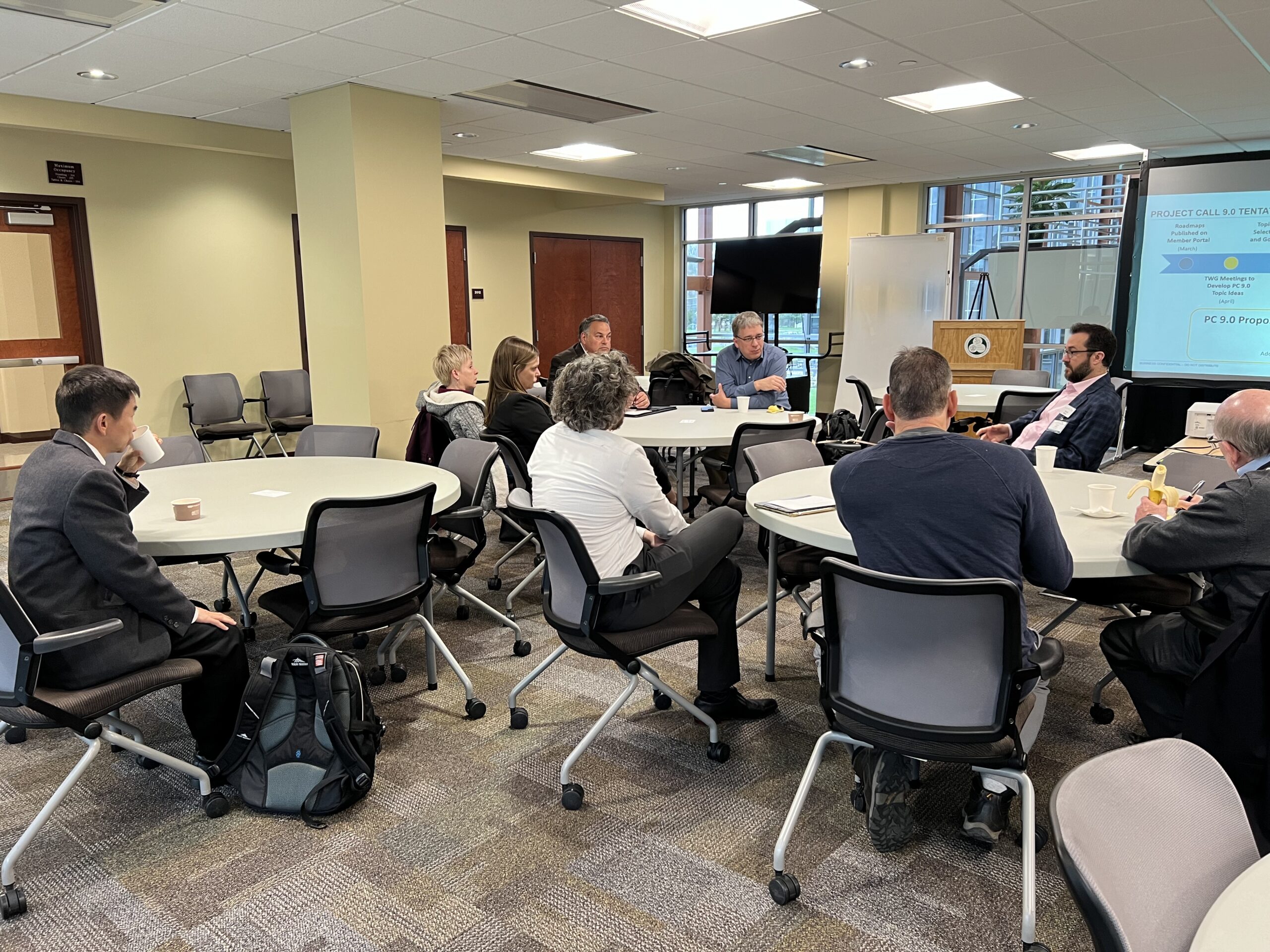
Technical Working Groups
Via a series of technical working groups (TWGs), NextFlex subject matter experts from across the U.S. manufacturing industry, academia, and government come together to collaborate on technology roadmaps, key technology gaps, and the necessary planning required to advance the hybrid electronics industrial base.
There are two types of Technical Working Groups: Manufacturing Thrust Areas and Technology Platform Demonstrators. The Manufacturing Thrust Areas are focused on advancing manufacturing technology and best practices while the Technology Platform Demonstrators are focused on applications.
Manufacturing Thrust Areas
- Device Integration & Packaging
- Materials
- Modeling & Design
- Printed Components & Microfluidics
- Standards, Test & Reliability
Technology Platform Demonstrators
- Automotive
- Asset Monitoring Systems
- Flexible Power
- Human Monitoring Systems
- Integrated Antenna Arrays
- Soft & Wearable Robotics
Each working group is led by a team of three co-leads, including one expert from each sector. Together, with over 150 additional diverse subject matter experts, the working groups use this collaborative space to determine where the Project Call focus and funding should be for technological advancement of advanced manufacturing and printed hybrid electronics.
View the NextFlex Hybrid Electronics Manufacturing Roadmap Summary here.
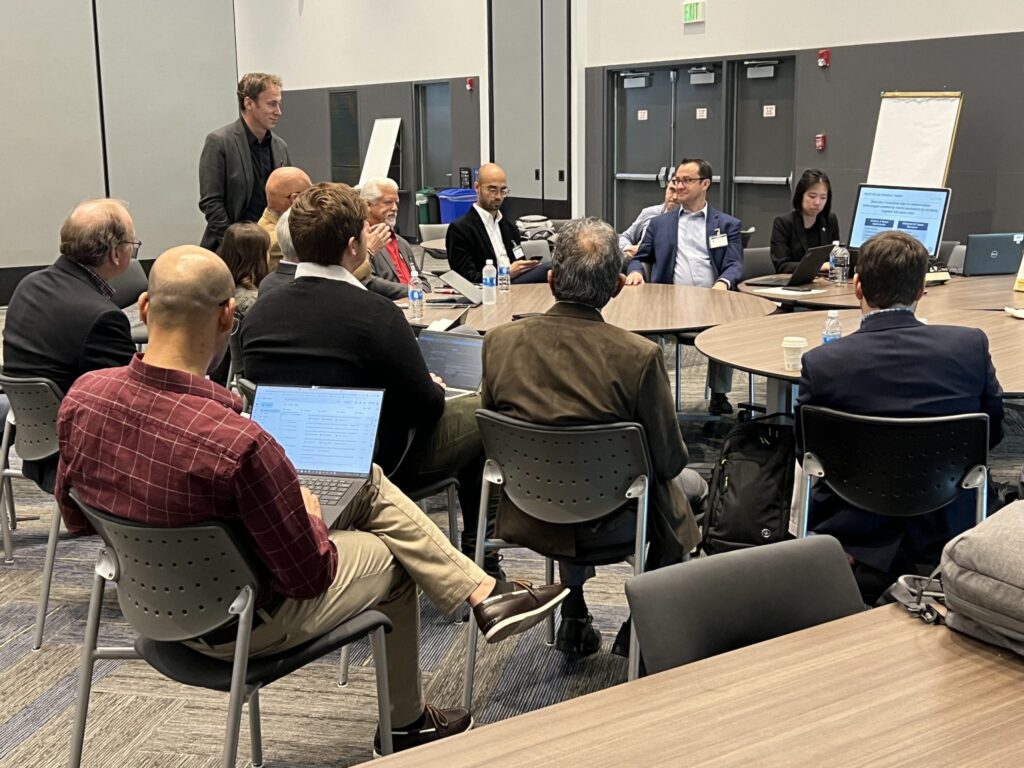
Current Focus Areas
Unobtrusive and minimally invasive wearable electronics for sensing and reporting physiological state of warfighters, athletes, geriatric populations, and medical patients in varied environments. Wearable electronics that accurately monitor several biomarkers while being comfortably worn or adhered to the subject’s skin.
Industry Co-Lead: Azar Alizadeh, GE Research; Academic Co-Lead: Jeff Morse, UMass Amherst; Government Co-Lead: Regina Shia, AFRL
Conformal electronics or integrated devices for sensing and reporting the state of infrastructure, vehicles, logistics, or the environment. Networks of sensors or devices for Internet of Things concepts.
Industry Co-Lead: Michael Mitchell, Boeing Research and Technology; Academic Co-Lead: Pradeep Lall, Auburn University; Government Co-Lead: Ken Blecker, ARDEC
Patterning of efficient printed wideband array antenna elements on flexible or conformal surfaces and integration of thinned electronics with printed wideband array elements. Applications in aeronautics, lightweight vehicles, or existing antenna structures.
Industry Co-Lead: Joseph Kunze, SI2 Technologies; Academic Co-Lead: Alkim Akyurtlu, UMass Lowell; Government Co-Lead: Steven Weiss, ARL
Soft, compressible sensors and devices for robotic functionality, enabling active clothing, wearable robots or robotic tools, and advanced prosthetics. Improved robot-human interactions for surgery, manufacturing, and consumer electronics.
Industry Co-Lead: Deepak Trivedi, GE; Academic Co-Lead: Chuck Zhang, Georgia Tech; Government Co-Lead: Nathan Lazarus, ARL
Power and energy storage subsystems for hybrid electronics devices including flexible batteries, supercapacitors, wireless power, and energy harvesting approaches. These devices are compatible with small, unobtrusive, flexible form factors.
Industry Co-Lead: David Mackanic, Anthro Energy; Academic Co-Lead: Devin MacKenzie, University of Washington; Government Co-Lead: Enoch Wang, Government
Development of new tools for handling and integrating thin flexible silicon dies, integrated circuits (ICs), passive components, and sensors on foldable, stretchable, flexible substrates and 3D surfaces. Leveraging advanced precision electronics printing and high-speed automated pick & place for integration of device components, interconnects, and data lines.
Industry Co-Lead: Nancy Stoeffel, GE; Academic Co-Lead: Stephen Gonya, Binghamton University; Academic Co-Lead: Mark Poliks, Binghamton University; Government Co-Lead: Darren Crum, NSWC Crane
& Microfluidics +
Developing and maturing contact and non-contact electronics printing processes that support hybrid electronics concepts, including sensors and discrete device components. Printing & integration of microfluidic channels and fluidic control elements.
Industry Co-Lead: Chris Stoessel, Eastman Chemical; Academic Co-Lead: Massood Atashbar, Western Michigan University; Government Co-Lead: Carrie Bartsch, AFRL
Supply scale-up and hybrid electronics manufacturing processes for conductive and dielectric inks and pastes, adhesives, encapsulant materials, and flexible substrates. Developing new materials with high conductivity to expand their use in hybrid electronics applications.
Industry Co-Lead: John Williams, Boeing Research and Technology; Academic Co-Lead: Joey Mead, UMass Lowell; Government Co-Lead: Haley Katz, Army DEVCOM; Government Co-Lead: Kate Duncan, CERDEC; Government Co-Lead: Chris Tabor, AFRL
Leveraging existing software & hardware design capabilities, simulation techniques, and manufacturing process control tools while also integrating novel manufacturing design rules for hybrid electronics.
Academic Co-Lead: Suresh Sitaraman, Georgia Tech; Government Co-Lead: Phil Buskohl, AFRL
Developing tools and test protocols to evaluate device-level and system-level hybrid electronics performance as well as reliability in both commercial and military environments. Partnering with standards organizations and professional societies to develop specifications & standards.
Industry Co-Lead: David Shaddock, GE; Academic Co-Lead: Mark Poliks, Binghamton University; Government Co-Lead: Emily Heckman, AFRL
The NextFlex Automotive Technical Working Group applies learnings from NextFlex projects and the efforts of other NextFlex working groups to increase the durability, reliability and performance of FHE-enabled automotive components, improve the travel range of vehicles via use of FHE-enabled components, and reduce the cost of FHE-enabled components.
Industry Co-Lead: Girish Wable, Jabil; Academic Co-Lead: Pradeep Lall, Auburn University; Government Co-Lead: Greg Wilford, ARDEC
Current Focus Areas
Unobtrusive and minimally invasive wearable electronics for sensing and reporting physiological state of warfighters, athletes, geriatric populations, and medical patients in varied environments. Wearable electronics that accurately monitor several biomarkers while being comfortably worn or adhered to the subject’s skin.
Industry Co-Lead: Azar Alizadeh, GE Research; Academic Co-Lead: Jeff Morse, UMass Amherst; Government Co-Lead: Regina Shia, AFRL
Conformal electronics or integrated devices for sensing and reporting the state of infrastructure, vehicles, logistics, or the environment. Networks of sensors or devices for Internet of Things concepts.
Industry Co-Lead: Michael Mitchell, Boeing Research and Technology; Academic Co-Lead: Pradeep Lall, Auburn University; Government Co-Lead: Ken Blecker, ARDEC
Patterning of efficient printed wideband array antenna elements on flexible or conformal surfaces and integration of thinned electronics with printed wideband array elements. Applications in aeronautics, lightweight vehicles, or existing antenna structures.
Industry Co-Lead: Joseph Kunze, SI2 Technologies; Academic Co-Lead: Alkim Akyurtlu, UMass Lowell; Government Co-Lead: Steven Weiss, ARL
Soft, compressible sensors and devices for robotic functionality, enabling active clothing, wearable robots or robotic tools, and advanced prosthetics. Improved robot-human interactions for surgery, manufacturing, and consumer electronics.
Industry Co-Lead: Deepak Trivedi, GE; Academic Co-Lead: Chuck Zhang, Georgia Tech; Government Co-Lead: Nathan Lazarus, ARL
Power and energy storage subsystems for hybrid electronics devices including flexible batteries, supercapacitors, wireless power, and energy harvesting approaches. These devices are compatible with small, unobtrusive, flexible form factors.
Industry Co-Lead: David Mackanic, Anthro Energy; Academic Co-Lead: Devin MacKenzie, University of Washington; Government Co-Lead: Enoch Wang, Government
Development of new tools for handling and integrating thin flexible silicon dies, integrated circuits (ICs), passive components, and sensors on foldable, stretchable, flexible substrates and 3D surfaces. Leveraging advanced precision electronics printing and high-speed automated pick & place for integration of device components, interconnects, and data lines.
Industry Co-Lead: Nancy Stoeffel, GE; Academic Co-Lead: Stephen Gonya, Binghamton University; Academic Co-Lead: Mark Poliks, Binghamton University; Government Co-Lead: Darren Crum, NSWC Crane
& Microfluidics
Developing and maturing contact and non-contact electronics printing processes that support hybrid electronics concepts, including sensors and discrete device components. Printing & integration of microfluidic channels and fluidic control elements.
Industry Co-Lead: Chris Stoessel, Eastman Chemical; Academic Co-Lead: Massood Atashbar, Western Michigan University; Government Co-Lead: Carrie Bartsch, AFRL
Supply scale-up and hybrid electronics manufacturing processes for conductive and dielectric inks and pastes, adhesives, encapsulant materials, and flexible substrates. Developing new materials with high conductivity to expand their use in hybrid electronics applications.
Industry Co-Lead: John Williams, Boeing Research and Technology; Academic Co-Lead: Joey Mead, UMass Lowell; Government Co-Lead: Haley Katz, Army DEVCOM; Government Co-Lead: Kate Duncan, CERDEC; Government Co-Lead: Chris Tabor, AFRL
Leveraging existing software & hardware design capabilities, simulation techniques, and manufacturing process control tools while also integrating novel manufacturing design rules for hybrid electronics.
Academic Co-Lead: Suresh Sitaraman, Georgia Tech; Government Co-Lead: Phil Buskohl, AFRL
Developing tools and test protocols to evaluate device-level and system-level hybrid electronics performance as well as reliability in both commercial and military environments. Partnering with standards organizations and professional societies to develop specifications & standards.
Industry Co-Lead: David Shaddock, GE; Academic Co-Lead: Mark Poliks, Binghamton University; Government Co-Lead: Emily Heckman, AFRL
The NextFlex Automotive Technical Working Group applies learnings from NextFlex projects and the efforts of other NextFlex working groups to increase the durability, reliability and performance of FHE-enabled automotive components, improve the travel range of vehicles via use of FHE-enabled components, and reduce the cost of FHE-enabled components.
Industry Co-Lead: Girish Wable, Jabil; Academic Co-Lead: Pradeep Lall, Auburn University; Government Co-Lead: Greg Wilford, ARDEC