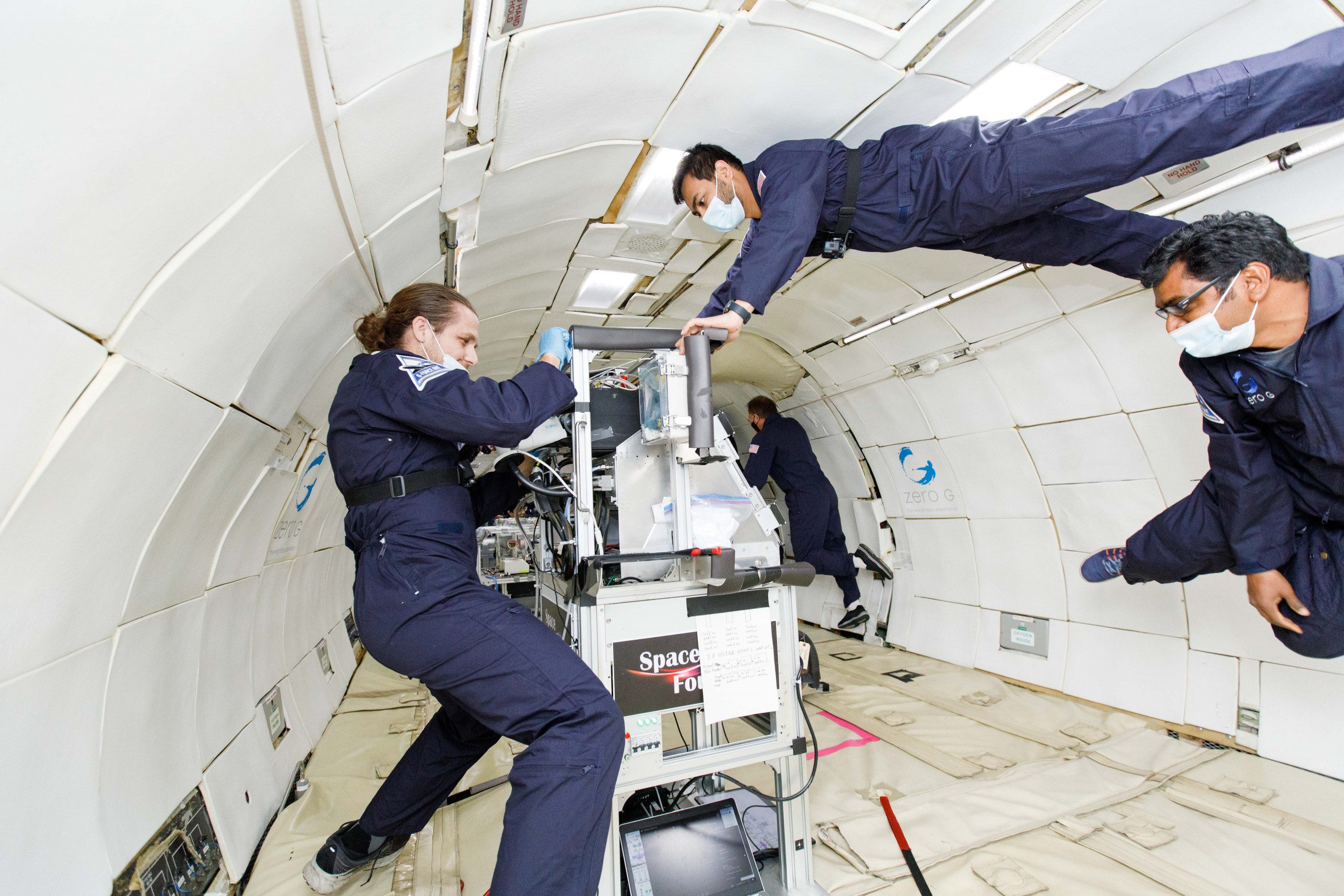
Printing on Flexible Substrates and Beyond!
Solving the Supply Problem with Factories in Space will Advance Exploration
by Dr Ram Prasad Gandhiraman, Space Foundry Founder and Chief Executive Officer | Photographs courtesy of Zero Gravity Corporation
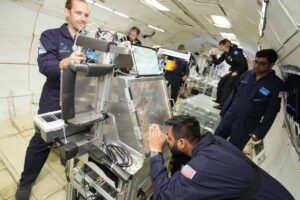
Space Foundry team member Dennis Nordlund works on the plasma jet printing technology test machine in the aircraft with Space Foundry team members close by.
The zero-gravity environment of space presents inherent obstacles in performing day-to-day tasks and this is something scientists have been grappling with for decades. Satellite technology, human exploration, the milestones overcome in this industry are countless. One major challenge that has arisen for the expansion of space exploration is cargo and supplies. In-space manufacturing focuses on developing radically different on-demand local manufacturing infrastructure for enabling future deep space exploration missions. Local manufacturing of materials, processes and technologies allows efficient recycling in space instead of sending everything from Earth.
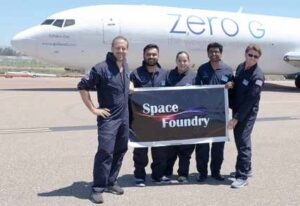
Standing outside the Zero-G Corporation aircraft that took them on the parabolic flights to simulate microgravity, the Space Foundry team members are (left to right), Dennis Nordlund, Pranay Doshi, Arlene Lopez, Ram Gandhiraman and Daniel Gutierrez.
This would tremendously reduce cost and logistics while avoiding potential mission delays due to missing or broken parts and components. In particular, the process of printing in zero-gravity can be a game changer for in-space manufacturing. The typical printing process for printed electronics uses ink dispensing printers that rely on ink and patterns to cure a layer of thickness with ultraviolet and high heat. The curing process takes a significant amount of time and needs a reducing environment in conjunction with high quality inks, limiting the use cases to only a perfect set of circumstances. Using printing in space would seem to be challenging considering that all the infrastructure needed is pretty much impossible to accommodate in a space setting. The space environment does not fall into an ideal subset. Given the limited infrastructure that astronauts have access to, many obstacles have to be overcome such as solving the problem of ink shelf-life issues and eliminating curing entirely. Only with such problems solved can the printing in space process go to the next level of ubiquity in orbit.
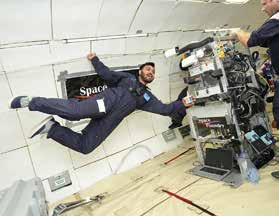
Space Foundry team member Pranay Doshi hangs on to the plasma jet printing technology test stand during a zero-g part of the parabolic flight.
Enter Space Foundry’s atmospheric pressure plasma jet technology. The addition of plasma to the printing process tailors the material properties while remaining situated in their original location. It can direct the materials to a substrate and primes the substrate for better adhesion without any curing of the inks. Ultimately, this opens the door to printing conductors and dielectrics on flexible substrates. Space Foundry is working with NASA through an active small business innovation and research award. The firm’s 3D printer will eventually be installed on the International Space Station to begin printing within the harsh environment space provides.
GAME CHANGER
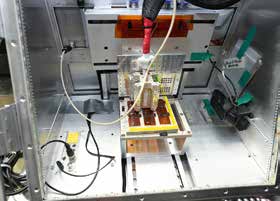
The plasma jet printing technology test machine.
These processes and technological advancements in printing systems will be a gamechanger for further space exploration providing ready access to critical materials for missions while enabling a low Earth orbit economy. Space Foundry has successfully demonstrated its plasma jet printing technology in microgravity on G-Force One, a specially modified Boeing 727-200 used for parabolic flights and operated by the Zero Gravity Corporation. Within the test, the team printed silver lines, pads, interdigitated electrodes, and a functioning Wi-Fi-antenna using a plasma jet printer. The success of that flight test led to more testing with different sets of materials. Most recently this included a copper ink developed by the company to maintain a longer shelf-life than traditional inks.
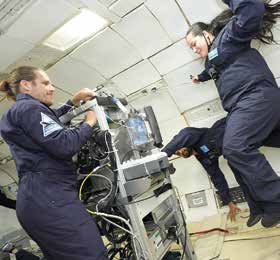
Space Foundry team members (left to right) Dennis Nordlund, Pranay Doshi and Arlene Lopez float in the zero-g environment.
With each successful flight a new set of materials will continue to be tested pushing the current limits on the 3D printing process. Space Foundry has accomplished all this with the help of a national initiative centered around defense manufacturing community support. It has been administered by the California Advanced Defense Ecosystems & National Consortia Effort (CADENCE) and the California Governor’s Office of Planning and Research (OPR). NextFlex, the United States’ flexible hybrid electronics manufacturing institute, has also helped Space Foundry. The firm is a member company of NextFlex and the institute has provided
advice and manufacturing assistance for flexible hybrid electronics. One of Space Foundry’s standalone printers has been installed at the NextFlex fabrication facility.
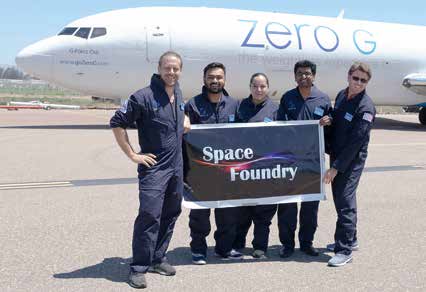