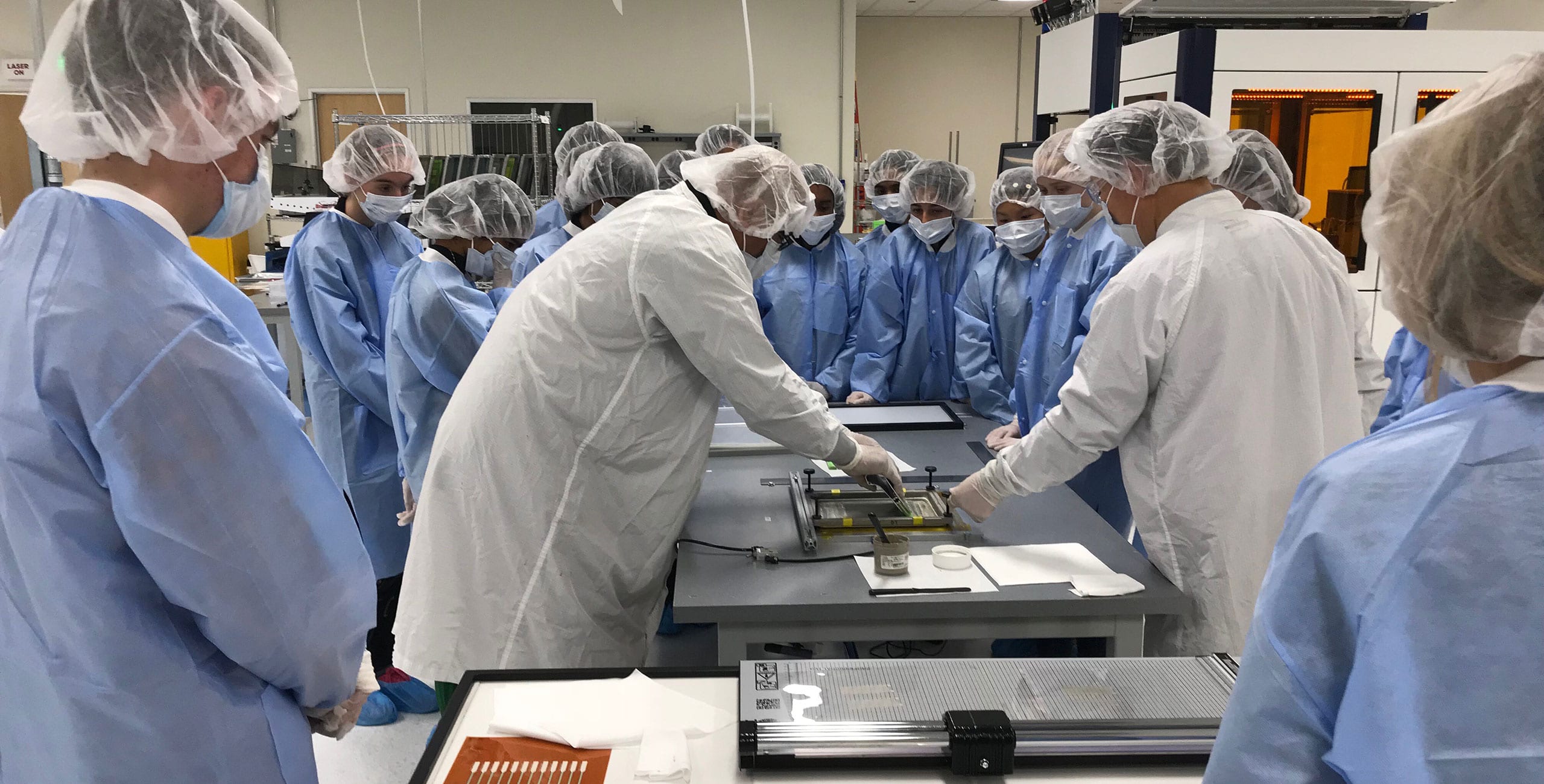
Success Story: Space Foundry
Overview
NextFlex, America’s Flexible Hybrid Electronic (FHE) Manufacturing Institute, has a state-of-the-art Technology Hub capable of fabricating fully integrated FHE devices and systems utilizing advanced manufacturing processes and tools. These processes and tools are continuously re-evaluated and applied in novel ways to improve the manufacturability of FHE and expand the potential applications of this technology.
Space Foundry Inc. – a small business with an active SBIR Phase II award from NASA – is an equipment manufacturer providing solutions for printing conductors and dielectrics on flexible substrates. Space Foundry has developed atmospheric pressure plasma jet technology to print electronic materials on both flexible and non-planar substrates. Aerosolized ink travels through the print head where the plasma is generated. The plasma helps in tailoring the material properties in-situ, directs the materials to the substrate, and primes the substrate for better adhesion. This unique technology has potential to reduce dependence on high quality inks, eliminate process steps (curing of inks), and expand the portfolio of materials that can be printed as well as printed on.
The wide range of potential applications provided by the plasma jet printer also increases the amount of process development work needed as variables (ink, substrate, and application) are iterated. To accelerate the development of Space Foundry’s technology and processes, reliable and frequent access to the plasma jet printer in a clean room space is needed. Installing a stand-alone printer in the NextFlex Fab will minimize environmental impacts on prints and increase time on the equipment by providing access to Space Foundry and NextFlex engineers.
Characterization of the prints produced on the plasma jet printer will also accelerate development. Subject matter experts and test equipment at the Technology Hub will provide data and direction for Space Foundry to tailor their equipment for FHE. Increased access for process development and improved data collection will improve the development feedback loop and bring new capabilities to FHE manufacturing and applications.
NextFlex’s Role
NextFlex had integrated Space Foundry plasma printer heads with a NextFlex-developed 6-axis robot with the future intent of incorporation in
another large format structural electronics integration platform. As part of the CADENCE Grant, NextFlex supported Space Foundry’s continued technology development by providing working space and resources and assisted the characterization of Space Foundry’s plasma jet printed samples.
NextFlex provided lab space and facilities accommodations for the installation and operation of Space Foundry’s stand-alone plasma jet printer; this accommodation included providing power, gases (providing the aerosol-assisted atmospheric pressure for plasma-based deposition), select raw materials, as well as the necessary facilities modifications to affect safe operation. NextFlex installed the Space Foundry standalone plasma printer and provided regular scheduled access to the Technology Hub to operate and evaluate the plasma jet printing platform. NextFlex also provided NextFlex engineers and technicians to be trained on the safe operation of the equipment – in order to improve support and lab safety – and to assist in the calibration, characterization, and operation of the platform.
NextFlex assisted in the characterization of Space Foundry’s plasma jet printed samples which would later be used in conjunction with Space Foundry’s NASA-funded SBIR. NextFlex provided the printed antenna design to facilitate the characterization and baseline performance of the plasma jet sample.
Benefits
Space Foundry successfully demonstrated its plasma jet printing technology in microgravity on G-FORCE ONE, a specially modified Boeing 727-200 using parabolic flight which was operated by Zero Gravity Corporation. The Space Foundry team printed silver lines, pads, interdigitated electrodes, and a Wi-Fi-antenna using a plasma jet printer. The Space Foundry plasma printer is a multilateral printing platform that can print a wide range of materials including metals, dielectrics, organics, and bio-inks. Plasma jet printing technology is based on the interaction between an aerosolized ink and a plasma. By carefully controlling the plasma process, the electronic structure of the ink materials can be tailored, and the oxidation state of the metals can be precisely controlled. With this success, Space Foundry is poised to enhance NASA’s In Space Manufacturing efforts through On Demand Manufacturing of Electronics (ODME), part of the Game Changing Development Program. Plasma jet printing can potentially be used for commercialization of low earth orbit and for manufacturing on the lunar surface. This technology is also a gamechanger for aerospace and defense customers who are interested in direct-write printing on complex non-planar objects for aircraft and missiles. The flights were supported by an SBIR Phase II-E award, funded jointly by NASA SBIR and the NASA Flight Opportunities Program. NextFlex has been supporting Space Foundry for antenna design and characterization. NextFlex is providing support through the “Defense Manufacturing Community Support Program,” administered by CADENCE through the California Governor’s Office of Planning and Research (OPR). The goal of this program is to support California’s defense innovation and manufacturing ecosystem through small business development.
For more information, please contact info@nextflex.us