Tech Hub Services
Today’s leading consumer, medical, communications, industrial and automotive products are increasing demand for all kinds of devices: MEMS sensors and actuators, power, microfluidic and photonic devices, technologies for ADAS (Advanced Driver Awareness and Safety), and more. Now, with the addition of hybrid electronics, an entirely new generation of devices is emerging – devices and platforms that will deliver on the promise of the Internet of Things (IoT).
In support of our mission to advance hybrid electronics manufacturing in the U.S., our facility has two cleanrooms and lab space for electronics printing, device integration and testing and measurement, that are fully compliant with ITAR’s (International Traffic in Arms Regulations) quality standard requirements for military electronics, materials, and guidance equipment manufacturing as well as the Food and Drug Administration’s (FDA) medical device manufacturing Quality Systems Regulations (QSR) for good manufacturing practices.
Working with NextFlex, a robust community of innovators including start-up companies and established manufacturers alike, are benefiting from a collaborative approach to electronics design, development and problem-solving via our state-of-the-art hybrid electronics technology hub. You can view the equipment list here.
Offering a full complement of hybrid electronics design, development and manufacturing services, the NextFlex Technology Hub provides the following capabilities:
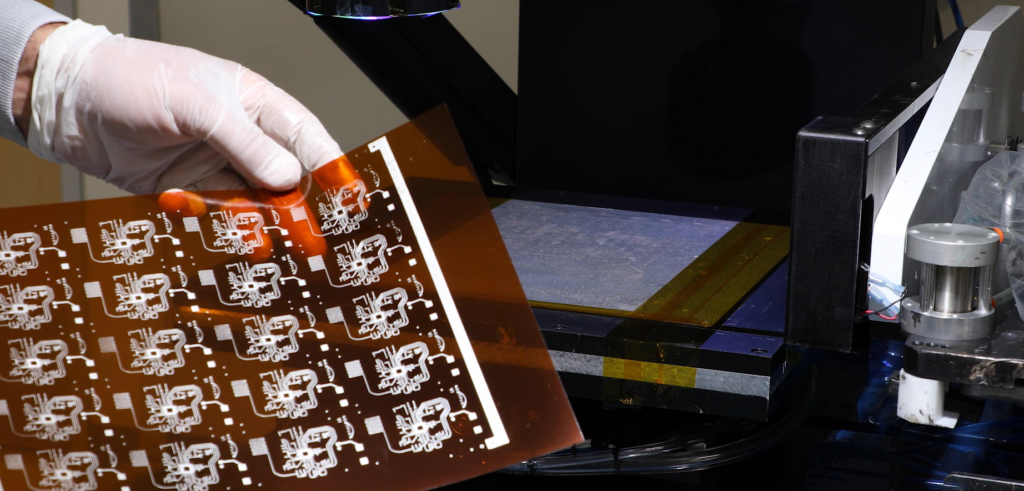
TECHNICAL CAPABILITIES
NextFlex’s team of engineers can help you with mechanical design, electrical design, design for manufacturing (DFM), and simulation. We have experience with novel design methods for RF and antenna printing.
In the NextFlex Print Lab, you have access to machines for screen, inkjet, aerosol jet, gravure offset, and extrusion printing with materials like silver, silver – silver chloride (Ag/AgCl), copper, or carbon inks, to substrates up to 200 x 300 mm (8” x 12”) including PET, PI, TPU, and biodegradable paper-like substrates.
The NextFlex Assembly Lab gives you access to machines for die attach methods including flip chip, pads up for wire bond (or printed) interconnects, and packaged (WLCSP) components; encapsulation; and surface mount technology (SMT, tape and reel pick-and-place), including multiple dispense processes with multiple types of adhesives.
Using laser processing equipment, NextFlex can help you with via drilling, laser ablation, substrate marking, and singulation.
NextFlex’s Test Lab has tools for a large variety of testing for electrical including RF and signal generation, for mechanical including stretch, fold, twist, and shear, and for environmental testing including temperature cycling, temperature and humidity, and sun exposure.
We can help you streamline your manufacturing processes, allowing you to reduce cost and maximize efficiency.
NextFlex engineers can help you with application development for iOS, Android, Windows, and more.
NextFlex can manufacture small-scale runs of your devices to prove manufacturability and help understand needs for scaling up production.
TECHNICAL CAPABILITIES
NextFlex’s team of engineers can help you with mechanical design, electrical design, design for manufacturing (DFM), and simulation. We have experience with novel design methods for RF and antenna printing.
In the NextFlex Print Lab, you have access to machines for screen, inkjet, aerosol jet, gravure offset, and extrusion printing with materials like silver, silver – silver chloride (Ag/AgCl), copper, or carbon inks, to substrates up to 200 x 300 mm (8” x 12”) including PET, PI, TPU, and biodegradable paper-like substrates.
The NextFlex Assembly Lab gives you access to machines for die attach methods including flip chip, pads up for wire bond (or printed) interconnects, and packaged (WLCSP) components; encapsulation; and surface mount technology (SMT, tape and reel pick-and-place), including multiple dispense processes with multiple types of adhesives.
Using laser processing equipment, NextFlex can help you with via drilling, laser ablation, substrate marking, and singulation.
NextFlex’s Test Lab has tools for a large variety of testing for electrical including RF and signal generation, for mechanical including stretch, fold, twist, and shear, and for environmental testing including temperature cycling, temperature and humidity, and sun exposure.
We can help you streamline your manufacturing processes, allowing you to reduce cost and maximize efficiency.
NextFlex engineers can help you with application development for iOS, Android, Windows, and more.
NextFlex can manufacture small-scale runs of your devices to prove manufacturability and help understand needs for scaling up production.
Application Areas
With a rapid push toward fly by wire and unmanned platforms, the aerospace industry has sought a variety of technological developments to impact communication systems, navigation & surveillance systems, flight control & management systems, mission/tactical systems, and electrical & emergency systems. And because the enabling technology must be streamlined for speed and light-weight for cost, hybrid electronics finds itself front and center in the evolution of the industry. Similarly, the use of Unmanned Aerial Vehicles (UAV) in commercial applications for monitoring, surveying and mapping, precision agriculture, and aerial remote sensing is resulting in even greater increased demand for hybrid electronics components.
From the 77GHz radar range-finding for automotive, to electronic warfare systems to wideband satellite communications to 5G connectivity, or BTLE enabled wearable electronics, or IOT protocols like SigFox and LORA or even true mesh networks, RF is one area where hybrid electronics growth continues to accelerate. As a result of this escalating demand for radio frequency components and innovative materials used in manufacturing these devices, NextFlex is playing a lead role in multiple segments within the RF and communications space building everything from NFC and BTLE devices, to complex AESA structures for electronic warfare.
Hybrid Electronics is enabling ultrathin and flexible, wearable electronics that can sample biomarkers in sweat, tears, saliva and interstitial fluid as well as conventional skin surface sensors. Through new ways to manufacture wearable electronics, intelligent devices, and integrated sensor fusion approaches, printed hybrid electronics are enabling medical quality data that ties to gold standards in the medical community. These new devices and wearable electronics encompass a broad range of products addressing both consumer and industrial applications and include everything from sports and activity trackers, to healthcare monitors, smart clothing, watches and glasses, and wearable 3D motion trackers.
As vehicles continue to get smarter and more electronically complex, new challenges are being introduced throughout the development process. Factor in consumer preference considerations and increasing safety requirements, plus the need for savvy and skilled electronics design, prototyping and pilot scale manufacturing capabilities are growing within the automotive PCB market. Early hybrid electronics applications are addressing everything from Advanced Driver Assistance Systems (ADAS) and basic automotive safety components that utilize FHE, to body comfort and vehicle lighting and powertrain systems.
Soft robotics are enabling high adaptability and flexibility for accomplishing routine tasks in addition to the improved safety when working with, and around, humans especially in a manufacturing environment. Robotic exoskeletons designed for giving mobility back to those who have lost it and/or assisting with moving and lifting objects to reduce workplace injury are prime examples of early soft robotic applications. Similarly, assistive soft robotics are proving useful to first responders and medical technicians for providing safer and better handling of patients and incapacitated individuals.
HEALTH MONITORING +
As infrastructure ages and complex systems such as commercial airlines require increased maintenance to keep them operational, intelligent systems that can trigger maintenance and improvements based on the actual state of wear have become essential. These newly developed asset monitoring solutions are able to monitor the structural integrity of everything from bridges, buildings, dams, levees, tunnels and other civil infrastructure, to aircraft, wind turbines, and other large structures. The asset monitoring market includes applications impacting civil infrastructure, aerospace & defense, energy, mining, and industrial machinery, automotive, transportation, and marine structures.
Application Areas
With a rapid push toward fly by wire and unmanned platforms, the aerospace industry has sought a variety of technological developments to impact communication systems, navigation & surveillance systems, flight control & management systems, mission/tactical systems, and electrical & emergency systems. And because the enabling technology must be streamlined for speed and light-weight for cost, hybrid electronics finds itself front and center in the evolution of the industry. Similarly, the use of Unmanned Aerial Vehicles (UAV) in commercial applications for monitoring, surveying and mapping, precision agriculture, and aerial remote sensing is resulting in even greater increased demand for hybrid electronics components.
From the 77GHz radar range-finding for automotive, to electronic warfare systems to wideband satellite communications to 5G connectivity, or BTLE enabled wearable electronics, or IOT protocols like SigFox and LORA or even true mesh networks, RF is one area where hybrid electronics growth continues to accelerate. As a result of this escalating demand for radio frequency components and innovative materials used in manufacturing these devices, NextFlex is playing a lead role in multiple segments within the RF and communications space building everything from NFC and BTLE devices, to complex AESA structures for electronic warfare.
Hybrid Electronics is enabling ultrathin and flexible, wearable electronics that can sample biomarkers in sweat, tears, saliva and interstitial fluid as well as conventional skin surface sensors. Through new ways to manufacture wearable electronics, intelligent devices, and integrated sensor fusion approaches, printed hybrid electronics are enabling medical quality data that ties to gold standards in the medical community. These new devices and wearable electronics encompass a broad range of products addressing both consumer and industrial applications and include everything from sports and activity trackers, to healthcare monitors, smart clothing, watches and glasses, and wearable 3D motion trackers.
As vehicles continue to get smarter and more electronically complex, new challenges are being introduced throughout the development process. Factor in consumer preference considerations and increasing safety requirements, plus the need for savvy and skilled electronics design, prototyping and pilot scale manufacturing capabilities are growing within the automotive PCB market. Early hybrid electronics applications are addressing everything from Advanced Driver Assistance Systems (ADAS) and basic automotive safety components that utilize FHE, to body comfort and vehicle lighting and powertrain systems.
Soft robotics are enabling high adaptability and flexibility for accomplishing routine tasks in addition to the improved safety when working with, and around, humans especially in a manufacturing environment. Robotic exoskeletons designed for giving mobility back to those who have lost it and/or assisting with moving and lifting objects to reduce workplace injury are prime examples of early soft robotic applications. Similarly, assistive soft robotics are proving useful to first responders and medical technicians for providing safer and better handling of patients and incapacitated individuals.
HEALTH MONITORING
As infrastructure ages and complex systems such as commercial airlines require increased maintenance to keep them operational, intelligent systems that can trigger maintenance and improvements based on the actual state of wear have become essential. These newly developed asset monitoring solutions are able to monitor the structural integrity of everything from bridges, buildings, dams, levees, tunnels and other civil infrastructure, to aircraft, wind turbines, and other large structures. The asset monitoring market includes applications impacting civil infrastructure, aerospace & defense, energy, mining, and industrial machinery, automotive, transportation, and marine structures.
Success Stories
Learn about some of NextFlex’s completed projects.

Confined Space Monitoring Armband
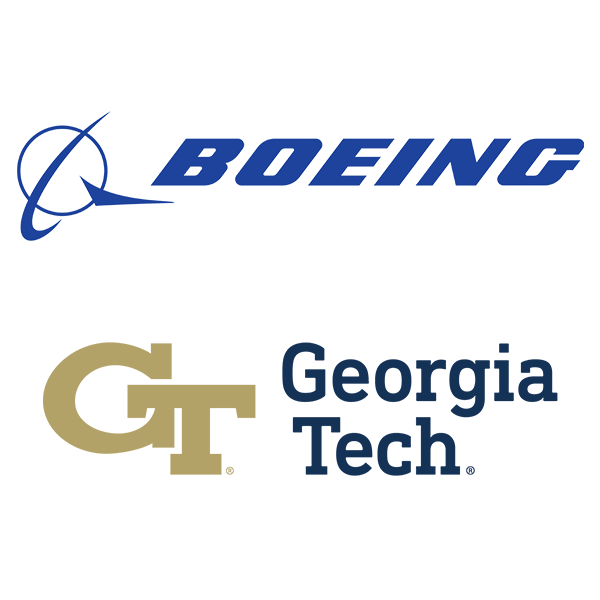
Flexible Antenna Array Technology (FAAT)

Wearable Platform for Medical Devices

Astrosense
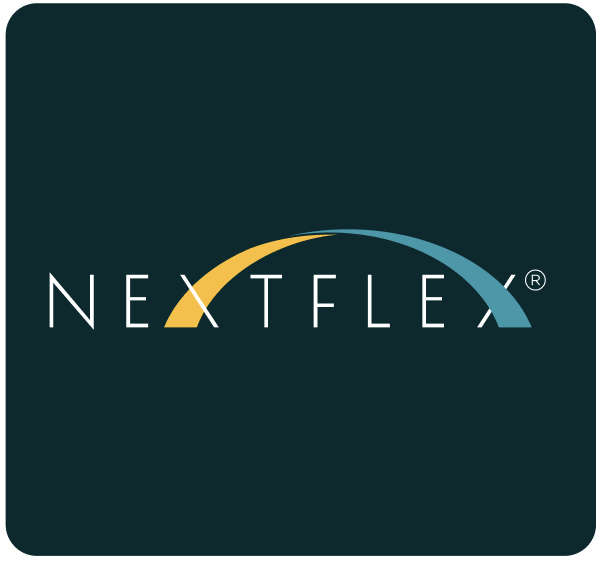
Flexible Microcontroller

Skin-worn Oxygen Monitor
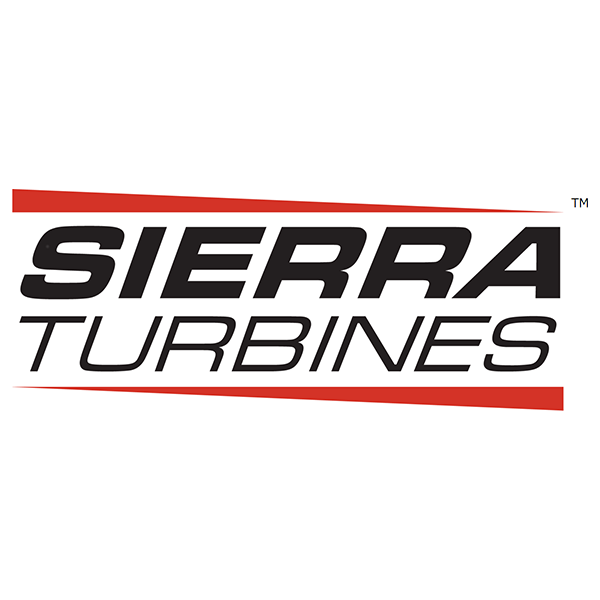
FHE-Fabricated SansEC Device
Overview
Every year, workers are injured and killed due to the build up carbon monoxide/dioxide and the high prevalence of volatile organic compounds while working in confined spaces. These problems are further compounded by the narrow entry and exit points from these spaces.
Current methods of monitoring worker health and safety in confined spaces rely on bulky atmospheric monitors and continuous visual observation. These methods are labor intensive and inaccurate, as they cannot monitor the atmosphere directly around the workers or indicate when workers are in a dangerous situation.
This problem has long been recognized by aircraft maintenance teams working on fuel tanks at Warner-Robbins Air Force Base. The team came to NextFlex for assistance in developing a wearable device to monitor the atmospheric levels surrounding workers in confined spaces.
Nextflex’s Role
With funding from the Air Force Research Laboratory (AFRL) and support from the maintenance team at Warner-Robbins Air Force Base, NextFlex developed a next generation Flexible Hybrid Electronics (FHE) confined space monitoring device. The device is designed as a flexible conformal armband capable of monitoring volatile organic compound concentrations, oxygen levels, temperature and humidity. Processing and communication are provided by a Bluetooth radio that can connect to a cell phone and allows for remote monitoring of the worker from a central control station. The design is powered by an onboard battery which can be wirelessly recharged using an embedded Qi charging circuit and brings together an incredibly dense array of features into a highly flexible, wearable and robust additively manufactured electronics format.
In addition to the high complexity of the design, significant effort has been placed into optimizing the antennas to maximize wireless range. Furthermore, the design was created to be highly secure, meeting FIPS 140-2 requirements, as well as meeting intrinsic safety requirements for explosion proofing in gaseous atmospheres.
“NextFlex has been highly innovative and responsive in working to advance the state-of-the-art in FHE in support of Air Force confined space maintenance requirements for an intrinsically safe, truly wearable atmospheric sensing capability which has been lacking to date. This AFRL-funded project builds on prior FHE advancements at NextFlex which enabled a flexible ‘Arduino®-like’ microcontroller and applies it to a real-world Air Force problem. They’ve refined this FHE microcontroller to operate CMOS gas sensors and added necessary power and comms to enable wearable chemical sensing in hazardous maintenance environments and replace handheld systems,” said Mathew Dalton, Research Chemist and Program Manager with Air Force Research Laboratory, Materials and Manufacturing Directorate. “Ultimately this will help keep maintainers safe while reducing costs and improving productivity!”
Benefits
When deployed, the FHE confined space monitoring armband designed by NextFlex will directly integrate into a framework already being deployed for the Air Force by Aptima Technologies. The armband will provide accurate and continuous monitoring of workers in highly confined spaces remotely. This new technology will reduce the number of personnel required to perform routine maintenance tasks, while simultaneously increasing the safety of the workers through monitoring of their working environment. By enabling unique monitoring wearables, FHE is helping NextFlex’s partners in the Air Force make the job safer for its personnel.
For more information, please contact info@nextflex.us
Overview
The Boeing Company and its partners the Georgia Institute of Technology (Georgia Tech), had a vision to build flexible antenna arrays using advanced flexible hybrid electronics (FHE) manufacturing. They partnered with NextFlex, a Manufacturing Innovation Institute with the shared goal of advancing U.S. manufacturing of FHE, to help develop mature multilayer patterning technologies for array antennas.
Nextflex’s Role
NextFlex provided funding support, technology insight and guidance to Boeing and Georgia Tech to produce printed carbon nanotubes and flexible ferrites, an array with surface adherence, flexible electronic packaging and low crosstalk feed technology. The partners tested the performance of antennas at various bends and environmental conditions to generate radio frequency (RF) data on printed transmission lines, a printed assembly of packaged low-noise amplifier (LNA) and printed magnetic film to ensure optimal coverage.
By combining expertise in FHE and advanced manufacturing, the partners developed a process to print antenna elements and a microstrip feed network on flexible hybrid substrates without vertical interconnect access greatly reducing fabrication time and costs. These multilayer antenna arrays include positive, negative, positive sourcing (PnP) electronics, patterned ferrites, environmental coatings to protect the arrays from harsh conditions and flex diodes and interconnects (ICs) to help the antennas transmit and receive signals from various angles. Collaboration between these companies initiated a fundamental foundation for advancement in FHE.
Benefits
With NextFlex’s support, Boeing and Georgia Tech were able to collaborate to take the developed FHE antenna design and fabrication methods and create 2×2, 4×4 and 8×8 printed panel antenna arrays. They have been able to respond to the accelerated adoption of wireless and FHE technologies in the digital aerial navigation era, moving towards the launch of FHE “skins” for UAVs to be used in advanced commercial and military applications.
For more information, please contact info@nextflex.us.
Overview
General Electric quickly recognized that wearables are increasingly becoming the future of both the technology and health sectors. With this forethought in mind, GE Global Research partnered with Binghamton University, the Rochester Institute of Technology, Infinite Corridor Technologies and NextFlex to develop a revolutionary, ubiquitous sensor systems for medical devices and to help combat the key fundamental challenges of integrating stretchable printed leads in wearables.
Nextflex’s Role
To accomplish this mission, GE Global Research and its partners came to America’s Flexible Hybrid Electronics (FHE) Manufacturing Innovation Institute, NextFlex, to craft FHE platform technologies for the fabrication of wireless, pervasive, and low-cost medical devices. With NextFlex’s support, they helped solve a major fundamental challenge of keeping device design and costs low through the implementation of FHE technology. The design approach addresses system partitioning between printed and standard flex, decreasing the wearable hardware size through FHE capability and addressing cost pressures. With flexible ECG electronics embedded deep within the printed sensor boards, the design is able to bend and move with the body while monitoring internal vital signs – critical to making a wearable functional for everyday use.
Key deliverables of this NextFlex funded project also included reporting on printing and characterization of RF components, reliability assessment of printed interconnections on various materials, including polyimide and thermoplastic polyurethane substrates, and interconnection methods for ball grid array devices to flex.
Benefits
With the assistance of NextFlex’s FHE expertise, GE Global Research is propelling the future of wearable tech through seamless integration, and has two prototype designs of wearable, wireless 3-lead ECG modules for clinical use. The combination of a flexible substrate with a health monitoring platform will accelerate the adoption of wireless and FHE technologies in the digital health era and pave way for more miniaturized, low cost wearables in the future.
For more information, please contact info@nextflex.us
Overview
NASA developed a next-generation wearable flexible sensor array for astronaut crew health monitoring, also known as “AstroSense”. Multi-disciplinary teams from Marshall Space Flight Center, Ames Research Center, and Flight Surgeons at Johnson Space Center all collaborated with NextFlex to design a wearable sensor array aimed at monitoring astronaut’s health and vital levels in space.
Nextflex’s Role
In the span of four months, the NextFlex team contributed to the development efforts of the next generation sensor for astronaut crew health monitoring by building and delivering a specific piece of hardware called a potentiostat for performing electrochemical analysis and printed disposable electrodes for use with artificial sweat samples. The team also performed biocompatibility tests, designed an encapsulating enclosure for moisture and dust ingress protection, and delivered several mock-up prototypes for demonstration purposes.
Benefits
With the support of NextFlex, the AstroSense device consists of two main components: a reusable electronic reader and a disposable electrode sensor. The reusable reader contains an antenna for wireless communication, electronic circuitry for data collection, processing and transmission for astronaut crew health monitoring, a coin battery and silicone encapsulant. The disposable electrode sensor consists of a flexible substrate with conductive electrodes and a stack of adhesives. The disposable sensor is attached to a reusable reader on one side and to human skin on other side. This next-generation wearable health monitor will allow NASA’s flight surgeons and health professionals to gain valuable data on the effect of stress upon the astronaut’s performance. This will lead to long-term improvements in the astronaut’s performance and overall health.
For more information, please contact info@nextflex.us.
Overview
The emerging technology field of additive, printed flexible hybrid electronics (FHE) promises to introduce a step change function in how electronics are manufactured and used, creating a product with superior mechanical and environmental properties compared to traditional processes at a lower overall price point.
As part of an FHE design and manufacturing demonstration project, NextFlex, in partnership with Air Force Research Lab (AFRL), translated electronic designs based on Arduino® products from standard PCB circuit boards to printed flex circuits. The effort is currently in its second phase.
Nextflex’s Role
NextFlex developed a process flow for manufacturing a flexible Arduino that reduced the number of process steps by almost two thirds when compared with traditional electronics manufacturing processes. NextFlex replaced the traditional circuit board with a thin, flexible plastic sheet and used digital printing processes for circuit elements. Die attach of a thin bare die eliminated traditional microcontroller packaging while further enabling flexibility of the product. The new process translates to an anticipated savings in manufacturing time and cost, as well as a significant reduction in the end-product weight – the flexible version is only a third of the weight of the rigid Arduino Mini board.
“The possibilities for FHE technology are virtually limitless,” said Dr. Benjamin Leever, the AFRL Advanced Development Team leader. “Proving the manufacturability of this technology through an open-source platform will expand FHE’s reach even further by providing everyone from industrial product developers to high school students with the opportunity to innovate on new electronics concepts.” He added, “We are pleased to have teamed with NextFlex on this project and look forward to the next steps in the optimization process. This is truly a momentous achievement for the FHE community.”
The NextFlex Flexible Microcontroller is now designed in as the base circuitry for several functional products for defense applications.
Benefits
With the design and manufacture of the NextFlex Flexible Microcontroller, several milestones in the additive manufacturing of printed electronics were achieved including:
- Development of design rules for the creation of printed FHE circuits
- Creation of high precision traces using a printing process for mounting of bare die ICs
- Development of a process for attachment of a bare die IC to a flexible substrate
- Integration of a 2.4GHz radio and printed RF antenna
Additionally, the automated manufacturing process for the flexible version both reduced the overall weight and the number of process steps by about two-thirds when compared to traditional board manufacturing. This demonstration project showed the suitability of additive printed circuit and FHE technology for the manufacture of basic embedded systems.
For more information, contact NextFlex at info@nextflex.us.
Overview
Profusa had a vision for its Lumee™ Oxygen Platform to be used in patients with potential acute and/or chronic changes in tissue oxygen levels who may benefit from continuous monitoring. Before it could be commercially available, Profusa had a key issue to resolve with the wearable reader of its injectable hydrogel sensor.
“Ten years ago, you couldn’t build a reader that could sense multiple signals and filter out the ‘noise’ of the body’s other signals, all while being small and skin-worn,” explains Ben Hwang, CEO of Profusa. “With the latest advancements in flexible hybrid electronics technology, it’s just mature enough to work the way we want — primarily because we selected the right domain expertise partner to work with, namely NextFlex.”
Nextflex’s Role
Rather than try and balance a complex development cycle across multiple R&D and manufacturing facilities, Profusa found a one-stop-shop solution at NextFlex’s Technology Hub in San Jose, which is also an FDA compliant manufacturing facility. Here, Profusa found it could develop its solution with NextFlex’s assistance in just four months while having the right conversations to move its reader design toward production at scale.
By combining expertise in flexible hybrid electronics, engineering, materials science and optics, NextFlex took Profusa’s design work and design criteria, and pushed them toward a smaller, flexible form that works in harmony with Profusa’s tissue sensors. In the end, improvements to durability, flexibility and performance were all achieved. NextFlex went on to manufacture over 1000 wearable units with increasing yield and productivity by the end of 2019.
Benefits
Through NextFlex’s aid, Profusa was able to take technology that could previously only be deployed in a hospital setting and move toward having a device with clinical-grade information in a wearable and flexible form that’s attractive to consumers. Profusa has been able to respond to the accelerated adoption of wireless and flexible hybrid electronics technologies in the digital health era, moving towards the launch of a wearable device that generates data that medical doctors and consumers can get the most out of.
For more information, please contact info@nextflex.us.
Overview
NextFlex, America’s Flexible Hybrid Electronic (FHE) Manufacturing Institute, has a state-of-the-art Technology Hub capable of fabricating fully integrated FHE devices and systems, utilizing advanced manufacturing processes and tools. The Technology Hub supports DoD as well as commercial electronics manufacturers by leveraging the benefits of FHE to reduce product costs, reduce product development cycle times, develop environmentally friendly manufacturing capabilities, and evaluate FHE equipment, substrates, materials, and components.
Sierra Turbines is a small California Defense contractor designing innovative, compact, high-efficiency turbines with features present in large scale commercial and military jet aircraft. Using additive manufacturing, they have developed a turbine engine which excels in reliability due to several design innovations such as a proprietary electronic control system, Engine Health Monitoring, and precision thermodynamic flows in both compression and combustion. Sierra Turbines’ initial market focus is on Unmanned Aerial Vehicles (UAVs) and ground based, hybrid electrical systems. Flexible Hybrid Electronics technology shows great promise and benefit to microturbine applications given the inherent nature of FHE structures with applications to structural health as well as asset and system performance monitoring.
Nextflex’s Role

A SansEC sensor consisting of silver spiral traces was conformally printed onto a 3D-printed Sierra Turbines part at NextFlex using an nScrypt printer.
Sierra Turbines proposed to leverage a SansEC sensing system from NASA Langley Research Center. SansEC is an open-circuit, resonant sensor that needs no electrical connections (thus the name SansEC or “without electrical connection”). The sensor structure consists of an array of conductive Archimedean spiral-like shapes printed onto a flexible substrate. NextFlex fabricated these samples by direct-write printing silver conductive traces onto a flexible substrate. Given device requirements from Sierra Turbines and Technology Hub capability, NextFlex developed the patterns, processes, and materials as well as fabricated prototype proof-of-concept samples of the SansEC sensors. Sierra Turbines, in turn, evaluated for purpose and application. NextFlex further fabricated another pattern, tuned to a specific Sierra Turbine application. Given the connection with NASA, NextFlex and Sierra Turbines made special consideration to NASA-compatible toolsets and materials in their down-selection.
Benefits
The successful demonstration of the FHE-fabricated SansEC device demonstrates the capability of adding electronic structures to manufactured parts using an advanced additive manufacturing process. The particular electronic structure, SansEC, can simultaneously measure different physical phenomena — temperature, fluid level, rotation rate, or wear, for example — and functions even when badly damaged. Previous variants of the SansEC sensors had been fabricated using traditional subtractive manufacturing methodologies and, as a consequence, do not have the reduced SWaP (size, weight, and power) attributes inherent for an FHE device. By demonstrating that FHE tools and processes can be applied to this particular electronic structure, Sierra Turbines is now positioned within the FHE ecosystem and supply chain. Asset monitoring and management and FHE technology will enable Sierra Turbines to competitively bid on SBIR’s modernization priorities related to Machine Learning, Autonomy, Controls, Microelectronics, and other applications related to defense and aerospace.
For more information, please contact info@nextflex.us.

Confined Space Monitoring Armband
Overview
Every year, workers are injured and killed due to the build up carbon monoxide/dioxide and the high prevalence of volatile organic compounds while working in confined spaces. These problems are further compounded by the narrow entry and exit points from these spaces.
Current methods of monitoring worker health and safety in confined spaces rely on bulky atmospheric monitors and continuous visual observation. These methods are labor intensive and inaccurate, as they cannot monitor the atmosphere directly around the workers or indicate when workers are in a dangerous situation.
This problem has long been recognized by aircraft maintenance teams working on fuel tanks at Warner-Robbins Air Force Base. The team came to NextFlex for assistance in developing a wearable device to monitor the atmospheric levels surrounding workers in confined spaces.
Nextflex’s Role
With funding from the Air Force Research Laboratory (AFRL) and support from the maintenance team at Warner-Robbins Air Force Base, NextFlex developed a next generation Flexible Hybrid Electronics (FHE) confined space monitoring device. The device is designed as a flexible conformal armband capable of monitoring volatile organic compound concentrations, oxygen levels, temperature and humidity. Processing and communication are provided by a Bluetooth radio that can connect to a cell phone and allows for remote monitoring of the worker from a central control station. The design is powered by an onboard battery which can be wirelessly recharged using an embedded Qi charging circuit and brings together an incredibly dense array of features into a highly flexible, wearable and robust additively manufactured electronics format.
In addition to the high complexity of the design, significant effort has been placed into optimizing the antennas to maximize wireless range. Furthermore, the design was created to be highly secure, meeting FIPS 140-2 requirements, as well as meeting intrinsic safety requirements for explosion proofing in gaseous atmospheres.
“NextFlex has been highly innovative and responsive in working to advance the state-of-the-art in FHE in support of Air Force confined space maintenance requirements for an intrinsically safe, truly wearable atmospheric sensing capability which has been lacking to date. This AFRL-funded project builds on prior FHE advancements at NextFlex which enabled a flexible ‘Arduino®-like’ microcontroller and applies it to a real-world Air Force problem. They’ve refined this FHE microcontroller to operate CMOS gas sensors and added necessary power and comms to enable wearable chemical sensing in hazardous maintenance environments and replace handheld systems,” said Mathew Dalton, Research Chemist and Program Manager with Air Force Research Laboratory, Materials and Manufacturing Directorate. “Ultimately this will help keep maintainers safe while reducing costs and improving productivity!”
Benefits
When deployed, the FHE confined space monitoring armband designed by NextFlex will directly integrate into a framework already being deployed for the Air Force by Aptima Technologies. The armband will provide accurate and continuous monitoring of workers in highly confined spaces remotely. This new technology will reduce the number of personnel required to perform routine maintenance tasks, while simultaneously increasing the safety of the workers through monitoring of their working environment. By enabling unique monitoring wearables, FHE is helping NextFlex’s partners in the Air Force make the job safer for its personnel.
For more information, please contact info@nextflex.us
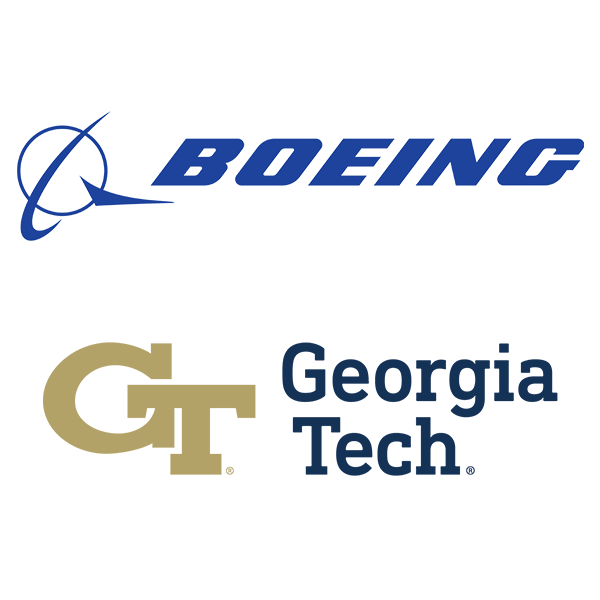
Flexible Antenna Array Technology (FAAT)
Overview
The Boeing Company and its partners the Georgia Institute of Technology (Georgia Tech), had a vision to build flexible antenna arrays using advanced flexible hybrid electronics (FHE) manufacturing. They partnered with NextFlex, a Manufacturing Innovation Institute with the shared goal of advancing U.S. manufacturing of FHE, to help develop mature multilayer patterning technologies for array antennas.
Nextflex’s Role
NextFlex provided funding support, technology insight and guidance to Boeing and Georgia Tech to produce printed carbon nanotubes and flexible ferrites, an array with surface adherence, flexible electronic packaging and low crosstalk feed technology. The partners tested the performance of antennas at various bends and environmental conditions to generate radio frequency (RF) data on printed transmission lines, a printed assembly of packaged low-noise amplifier (LNA) and printed magnetic film to ensure optimal coverage.
By combining expertise in FHE and advanced manufacturing, the partners developed a process to print antenna elements and a microstrip feed network on flexible hybrid substrates without vertical interconnect access greatly reducing fabrication time and costs. These multilayer antenna arrays include positive, negative, positive sourcing (PnP) electronics, patterned ferrites, environmental coatings to protect the arrays from harsh conditions and flex diodes and interconnects (ICs) to help the antennas transmit and receive signals from various angles. Collaboration between these companies initiated a fundamental foundation for advancement in FHE.
Benefits
With NextFlex’s support, Boeing and Georgia Tech were able to collaborate to take the developed FHE antenna design and fabrication methods and create 2×2, 4×4 and 8×8 printed panel antenna arrays. They have been able to respond to the accelerated adoption of wireless and FHE technologies in the digital aerial navigation era, moving towards the launch of FHE “skins” for UAVs to be used in advanced commercial and military applications.
For more information, please contact info@nextflex.us.

Wearable Platform for Medical Devices
Overview
General Electric quickly recognized that wearables are increasingly becoming the future of both the technology and health sectors. With this forethought in mind, GE Global Research partnered with Binghamton University, the Rochester Institute of Technology, Infinite Corridor Technologies and NextFlex to develop a revolutionary, ubiquitous sensor systems for medical devices and to help combat the key fundamental challenges of integrating stretchable printed leads in wearables.
Nextflex’s Role
To accomplish this mission, GE Global Research and its partners came to America’s Flexible Hybrid Electronics (FHE) Manufacturing Innovation Institute, NextFlex, to craft FHE platform technologies for the fabrication of wireless, pervasive, and low-cost medical devices. With NextFlex’s support, they helped solve a major fundamental challenge of keeping device design and costs low through the implementation of FHE technology. The design approach addresses system partitioning between printed and standard flex, decreasing the wearable hardware size through FHE capability and addressing cost pressures. With flexible ECG electronics embedded deep within the printed sensor boards, the design is able to bend and move with the body while monitoring internal vital signs – critical to making a wearable functional for everyday use.
Key deliverables of this NextFlex funded project also included reporting on printing and characterization of RF components, reliability assessment of printed interconnections on various materials, including polyimide and thermoplastic polyurethane substrates, and interconnection methods for ball grid array devices to flex.
Benefits
With the assistance of NextFlex’s FHE expertise, GE Global Research is propelling the future of wearable tech through seamless integration, and has two prototype designs of wearable, wireless 3-lead ECG modules for clinical use. The combination of a flexible substrate with a health monitoring platform will accelerate the adoption of wireless and FHE technologies in the digital health era and pave way for more miniaturized, low cost wearables in the future.
For more information, please contact info@nextflex.us

Astrosense
Overview
NASA developed a next-generation wearable flexible sensor array for astronaut crew health monitoring, also known as “AstroSense”. Multi-disciplinary teams from Marshall Space Flight Center, Ames Research Center, and Flight Surgeons at Johnson Space Center all collaborated with NextFlex to design a wearable sensor array aimed at monitoring astronaut’s health and vital levels in space.
Nextflex’s Role
In the span of four months, the NextFlex team contributed to the development efforts of the next generation sensor for astronaut crew health monitoring by building and delivering a specific piece of hardware called a potentiostat for performing electrochemical analysis and printed disposable electrodes for use with artificial sweat samples. The team also performed biocompatibility tests, designed an encapsulating enclosure for moisture and dust ingress protection, and delivered several mock-up prototypes for demonstration purposes.
Benefits
With the support of NextFlex, the AstroSense device consists of two main components: a reusable electronic reader and a disposable electrode sensor. The reusable reader contains an antenna for wireless communication, electronic circuitry for data collection, processing and transmission for astronaut crew health monitoring, a coin battery and silicone encapsulant. The disposable electrode sensor consists of a flexible substrate with conductive electrodes and a stack of adhesives. The disposable sensor is attached to a reusable reader on one side and to human skin on other side. This next-generation wearable health monitor will allow NASA’s flight surgeons and health professionals to gain valuable data on the effect of stress upon the astronaut’s performance. This will lead to long-term improvements in the astronaut’s performance and overall health.
For more information, please contact info@nextflex.us.
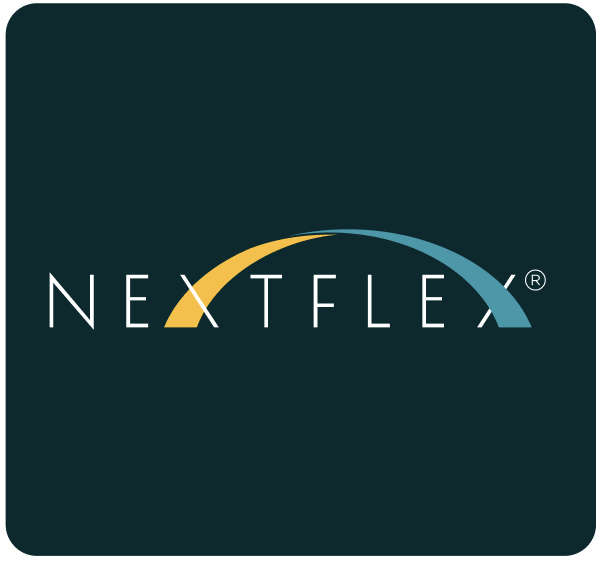
Flexible Microcontroller
Overview
The emerging technology field of additive, printed flexible hybrid electronics (FHE) promises to introduce a step change function in how electronics are manufactured and used, creating a product with superior mechanical and environmental properties compared to traditional processes at a lower overall price point.
As part of an FHE design and manufacturing demonstration project, NextFlex, in partnership with Air Force Research Lab (AFRL), translated electronic designs based on Arduino® products from standard PCB circuit boards to printed flex circuits. The effort is currently in its second phase.
Nextflex’s Role
NextFlex developed a process flow for manufacturing a flexible Arduino that reduced the number of process steps by almost two thirds when compared with traditional electronics manufacturing processes. NextFlex replaced the traditional circuit board with a thin, flexible plastic sheet and used digital printing processes for circuit elements. Die attach of a thin bare die eliminated traditional microcontroller packaging while further enabling flexibility of the product. The new process translates to an anticipated savings in manufacturing time and cost, as well as a significant reduction in the end-product weight – the flexible version is only a third of the weight of the rigid Arduino Mini board.
“The possibilities for FHE technology are virtually limitless,” said Dr. Benjamin Leever, the AFRL Advanced Development Team leader. “Proving the manufacturability of this technology through an open-source platform will expand FHE’s reach even further by providing everyone from industrial product developers to high school students with the opportunity to innovate on new electronics concepts.” He added, “We are pleased to have teamed with NextFlex on this project and look forward to the next steps in the optimization process. This is truly a momentous achievement for the FHE community.”
The NextFlex Flexible Microcontroller is now designed in as the base circuitry for several functional products for defense applications.
Benefits
With the design and manufacture of the NextFlex Flexible Microcontroller, several milestones in the additive manufacturing of printed electronics were achieved including:
- Development of design rules for the creation of printed FHE circuits
- Creation of high precision traces using a printing process for mounting of bare die ICs
- Development of a process for attachment of a bare die IC to a flexible substrate
- Integration of a 2.4GHz radio and printed RF antenna
Additionally, the automated manufacturing process for the flexible version both reduced the overall weight and the number of process steps by about two-thirds when compared to traditional board manufacturing. This demonstration project showed the suitability of additive printed circuit and FHE technology for the manufacture of basic embedded systems.
For more information, contact NextFlex at info@nextflex.us.

Skin-worn Oxygen Monitor
Overview
Profusa had a vision for its Lumee™ Oxygen Platform to be used in patients with potential acute and/or chronic changes in tissue oxygen levels who may benefit from continuous monitoring. Before it could be commercially available, Profusa had a key issue to resolve with the wearable reader of its injectable hydrogel sensor.
“Ten years ago, you couldn’t build a reader that could sense multiple signals and filter out the ‘noise’ of the body’s other signals, all while being small and skin-worn,” explains Ben Hwang, CEO of Profusa. “With the latest advancements in flexible hybrid electronics technology, it’s just mature enough to work the way we want — primarily because we selected the right domain expertise partner to work with, namely NextFlex.”
Nextflex’s Role
Rather than try and balance a complex development cycle across multiple R&D and manufacturing facilities, Profusa found a one-stop-shop solution at NextFlex’s Technology Hub in San Jose, which is also an FDA compliant manufacturing facility. Here, Profusa found it could develop its solution with NextFlex’s assistance in just four months while having the right conversations to move its reader design toward production at scale.
By combining expertise in flexible hybrid electronics, engineering, materials science and optics, NextFlex took Profusa’s design work and design criteria, and pushed them toward a smaller, flexible form that works in harmony with Profusa’s tissue sensors. In the end, improvements to durability, flexibility and performance were all achieved. NextFlex went on to manufacture over 1000 wearable units with increasing yield and productivity by the end of 2019.
Benefits
Through NextFlex’s aid, Profusa was able to take technology that could previously only be deployed in a hospital setting and move toward having a device with clinical-grade information in a wearable and flexible form that’s attractive to consumers. Profusa has been able to respond to the accelerated adoption of wireless and flexible hybrid electronics technologies in the digital health era, moving towards the launch of a wearable device that generates data that medical doctors and consumers can get the most out of.
For more information, please contact info@nextflex.us.
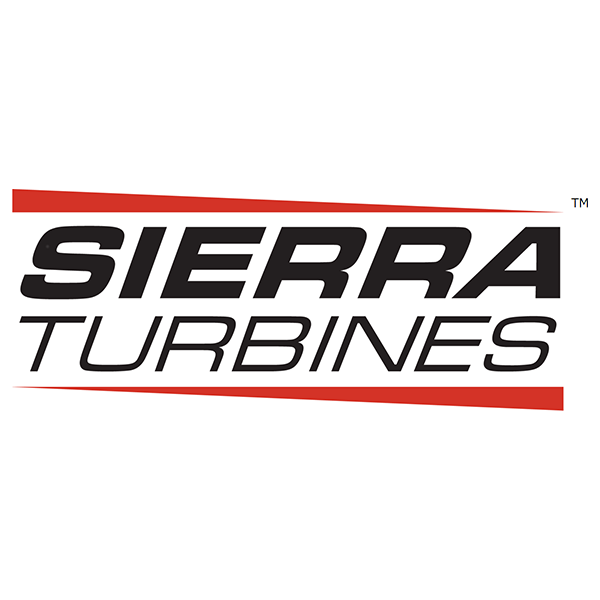
FHE-Fabricated SansEC Device
Overview
NextFlex, America’s Flexible Hybrid Electronic (FHE) Manufacturing Institute, has a state-of-the-art Technology Hub capable of fabricating fully integrated FHE devices and systems, utilizing advanced manufacturing processes and tools. The Technology Hub supports DoD as well as commercial electronics manufacturers by leveraging the benefits of FHE to reduce product costs, reduce product development cycle times, develop environmentally friendly manufacturing capabilities, and evaluate FHE equipment, substrates, materials, and components.
Sierra Turbines is a small California Defense contractor designing innovative, compact, high-efficiency turbines with features present in large scale commercial and military jet aircraft. Using additive manufacturing, they have developed a turbine engine which excels in reliability due to several design innovations such as a proprietary electronic control system, Engine Health Monitoring, and precision thermodynamic flows in both compression and combustion. Sierra Turbines’ initial market focus is on Unmanned Aerial Vehicles (UAVs) and ground based, hybrid electrical systems. Flexible Hybrid Electronics technology shows great promise and benefit to microturbine applications given the inherent nature of FHE structures with applications to structural health as well as asset and system performance monitoring.
Nextflex’s Role

A SansEC sensor consisting of silver spiral traces was conformally printed onto a 3D-printed Sierra Turbines part at NextFlex using an nScrypt printer.
Sierra Turbines proposed to leverage a SansEC sensing system from NASA Langley Research Center. SansEC is an open-circuit, resonant sensor that needs no electrical connections (thus the name SansEC or “without electrical connection”). The sensor structure consists of an array of conductive Archimedean spiral-like shapes printed onto a flexible substrate. NextFlex fabricated these samples by direct-write printing silver conductive traces onto a flexible substrate. Given device requirements from Sierra Turbines and Technology Hub capability, NextFlex developed the patterns, processes, and materials as well as fabricated prototype proof-of-concept samples of the SansEC sensors. Sierra Turbines, in turn, evaluated for purpose and application. NextFlex further fabricated another pattern, tuned to a specific Sierra Turbine application. Given the connection with NASA, NextFlex and Sierra Turbines made special consideration to NASA-compatible toolsets and materials in their down-selection.
Benefits
The successful demonstration of the FHE-fabricated SansEC device demonstrates the capability of adding electronic structures to manufactured parts using an advanced additive manufacturing process. The particular electronic structure, SansEC, can simultaneously measure different physical phenomena — temperature, fluid level, rotation rate, or wear, for example — and functions even when badly damaged. Previous variants of the SansEC sensors had been fabricated using traditional subtractive manufacturing methodologies and, as a consequence, do not have the reduced SWaP (size, weight, and power) attributes inherent for an FHE device. By demonstrating that FHE tools and processes can be applied to this particular electronic structure, Sierra Turbines is now positioned within the FHE ecosystem and supply chain. Asset monitoring and management and FHE technology will enable Sierra Turbines to competitively bid on SBIR’s modernization priorities related to Machine Learning, Autonomy, Controls, Microelectronics, and other applications related to defense and aerospace.
For more information, please contact info@nextflex.us.
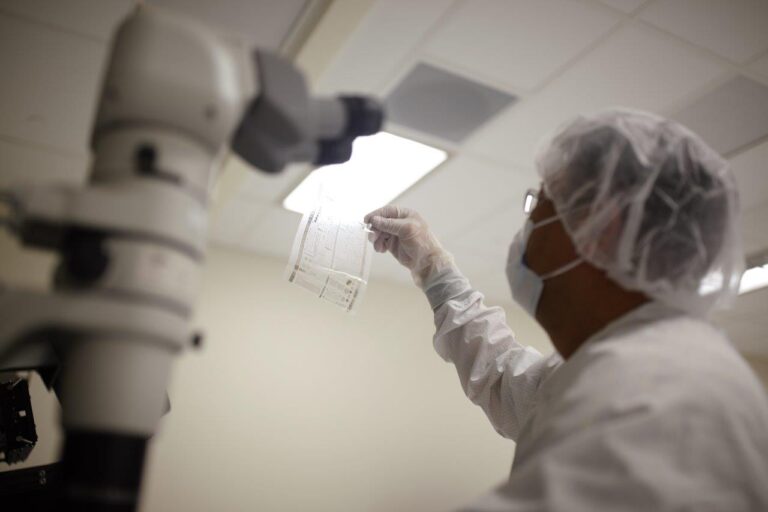
WORKING WITH NEXTFLEX
Our process:
- Identify your organization’s needs, contact NextFlex, and secure an NDA with our legal team.
- Take advantage of a preliminary call with our technical team to discuss how we can help you meet your needs.
- Develop a Statement of Work and Project Scope with our technical team. This helps generate a timeline and set expectations for the course of the project.
- If you already have a product design, contract with our team to have your product developed. If you have a concept but no design, our team can help you translate your ideas into design files that are ready for manufacturing. If you are looking for funding or manufacturing partners, join a teaming event and submit a proposal for our next Project Call. Throughout the contracting process, you can rest assured that your Intellectual Property is secure with our robust IP policy.
- Iterate with our team as your project needs change.
We can help you by:
- Mentoring/assisting qualified small- and medium-sized manufacturers, including providing engineering and design services.
- Supporting small business recipients in prototyping & developing proof of concept demonstrations for DoD projects.
- Helping organizations de-risk technology/capital equipment adoption by enabling the evaluation of tool capabilities that exist at the NextFlex technology hub for their applications prior to investing in new equipment.
- Providing manufacturing support from early prototype through low-volume manufacturing (if appropriate).
- Assisting with transitioning/scaling of production to a U.S. volume manufacturer.
Tell us how we can help by completing this form or sending an inquiry to info@nextflex.us:
Virtual Tour
Explore the NextFlex Technology Hub with this interactive virtual tour
